通过对国内外半球形锻件成形技术研究,利用公司现有设备(3 150t水压机).采用热模锻+热冲压的工艺路线成功的生产出Tc4半球形锻件(图1)。但由于TC4钛合金压力加工性能差。而且该钛锻件最终成形是在水压机上实现,并非专用的模锻机。这就造成在试制过程中存在生产能力小、锻件外形尺寸合格率偏低、成品率不高等问题。
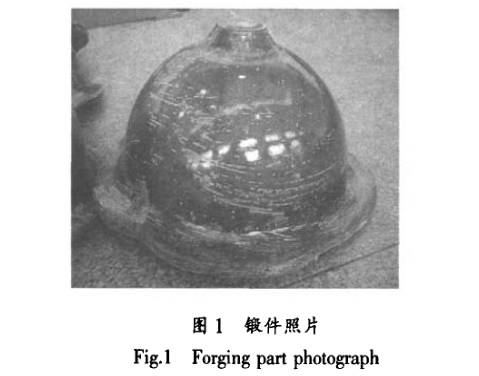
1、TC4半球钛体锻件存在的主要缺陷
通过对生产的半球形锻件进行缺陷整理。主要可归纳为以下5种缺陷:
(1)靠翻边处内径尺寸r偏大(见图2),造成用户机加后留有黑皮:

(2)靠翻边处外球面易出现较深裂纹;
(3)外表面出现微裂纹;
(4)成形后半球体出现偏斜;
(5)半球体在靠近气嘴处拉裂,甚至出现整体掉底现象。
2、TC4半球锻件生产工艺的改进
2.1 改进模具结构。利于金属流动
采用水压机生产锻件存在导向差的缺点。虽在设计模具时增加了导套以增加导向精度(见图3),但考虑到模具热胀冷缩,以及上、下模易于导入等因素的影响,导套单边仍留了一定间隙。
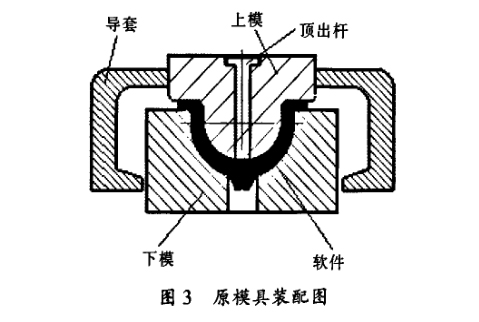
这就使生产时因为无法精确导向而可能造成坯料在成形时局部已与下模(原下模结构为依据锻件尺寸设计的半球形实体)接触,而上模继续向下拉深的现象(见图4)。由于坯
料与模具接触面积大,摩擦力大,以上现象一旦发生,仅靠半球形锻件成形过程自身不能实现找正,这就势必导致成形后的半球形锻件出现靠翻边处出现较深裂纹或锻件在偏斜现象。
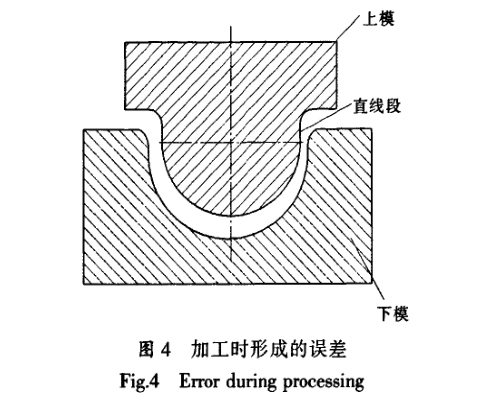
半球形锻件的最后成型过程可以看作是厚板拉深,据有关资料介绍。采用厚板拉深的此类半球形锻件可以采用悬空法拉深成形。此类成形模具结构较原成形模具结构在成形过程中更有利于金属的流动。同时由于成形过程中模具与坯料接触面积小,当上下模并未对正时,靠半球形锻件成形过程自我找正也可使模具找正。针对锻件存在的缺陷,改变了原下模结构,设计为悬空结构(见图5)。
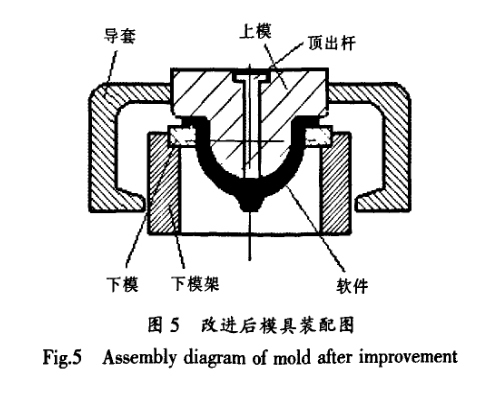
2.2 调整上模成形尺寸。提高半球形锻件外形尺寸根据参考资料【1】,上模直线段长度可按以下公式计算:
h=h1+h2,
其中:h为上模直线段长度;h1修边余量,一般取(1~2)t;t为坯料厚度;h2附加保险余量,一般为50~100mm。
考虑到该资料适用的材料中并无TC4钛合金,另外结合原设计模具的经验及生产实际情况,原上模直线段长度并不能补偿锻件在随后的热处理及冷却过程的回弹造成的靠翻边处内径尺寸偏大现象。而完全照搬资料。将直线段增加将近100mm左右。必然增加半球成形前坯料的直径。这就势必降低产品的成品率,同时随着坯料直径的增加。如不改变成形前坯料壁厚,必然改变成形稳定性(根据参考资料【1】,成形前坯料的壁厚/直径比值数值越小.成形区抗失稳的能力越差,越容易起皱)根据以往的生产实际情况,并进行几次试验。最终确定了上模的直线段长度,补偿了锻件在随后的冷却过程及热处理的回弹造成的靠翻边处内径尺寸偏大,确保了锻件尺寸不会由于回弹而造成超差。
2.3 选择合适涂层,改善成形润滑条件。
对半球成形前涂层的选择及涂刷方法进行了多次试验,曾试过A5玻璃粉、A5与M1混合使用等涂层(A5及Ml为涂层编号),最终选择我国自行研制的900~l 000℃使用的冲压用玻璃涂层,并且总结出了可行、有效的涂刷方法,改善了成形过程的润滑条件,更有利于成形过程金属的流动。同时使用了这种玻璃润滑剂,使最后成形时从出炉到成形完毕整个过程温降有所减少,从而使整个变形过程更加均匀,减少了成形后锻件表面出现裂纹的情况。
3、结束语
对TC4半球形锻件成形工艺改进后,已累计生产该锻件近千件,产品锻造合格率达到95%以上,实现了工业化生产。经过改进的成形工艺为中小型设备批量生产该类锻件提供了新的方法。
参 考文献
【1】锻压手册,中国机械工程学会塑性工程学会,机械工业出版社,1993,2.
相关链接