2010年,国家推出了振兴汽车工业、船舶产业、装备制造业、电子信息业等十大产业的规划,此规划带动了
国内汽车行业的高速发展,而汽车行业的发展必将带动国内汽车紧固件发展。面临着这样一个良好的发展契
机,国内汽车紧固件行业却无法满足汽车行业的生产需求:一方面原材料强度无法满足高强度紧固件的需求
,低强度紧固件市场饱和,而高强度异形紧固件长期依赖进口;另一方面企业技术薄弱,设备和人员更新慢
,无法满足高强度紧固件的生产需求。
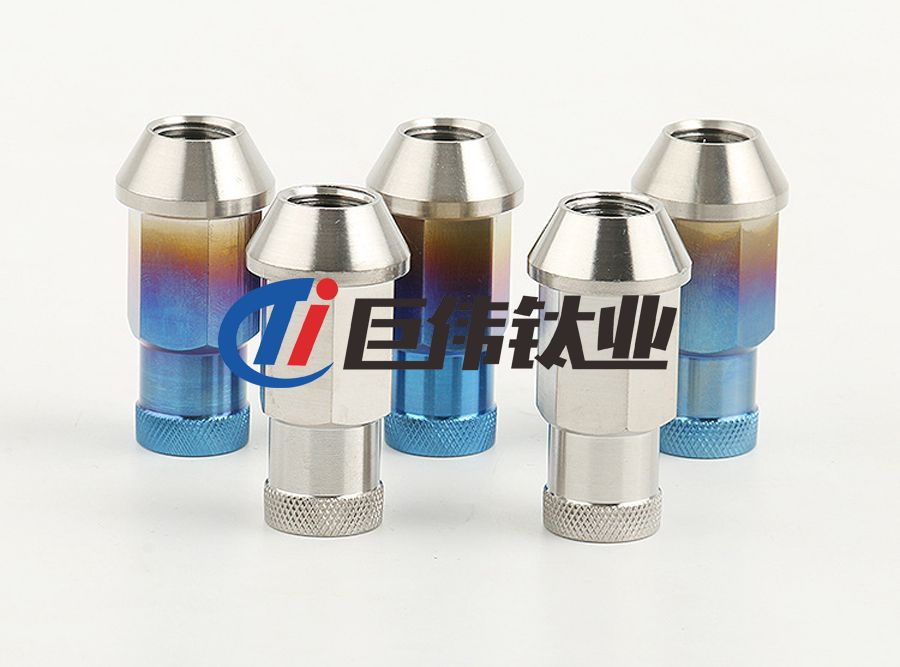
为了满足高强度紧固件的生产需求,先进的热处理装备是其必备条件,而先进的热处理工艺是影响其内在质
量的关键因素,二者缺一不可。目前我国汽车的高强度紧固件在质量、环保和能耗等方面仍处于落后的状态
,为了赶超国际先进水平,我国的高强度紧固件的开发和生产面临着严峻的考验。
1、汽车紧固件
从整个制造业的发展来看,紧固件被称为“工业之米”、国民经济的“螺丝钉”。紧固件在整个产品结构中
,通常只占很小的一部分,但作为产品的有机组成部分,却起着重要的作用:将产品结构中两个或两个以上
的工件紧固连接成一个整体。常见的紧固件有螺栓、螺钉、螺柱、螺母以及其组合件如垫圈、档圈、销、铆
钉、连接副等,广泛用于汽车、工程、建筑等领域。
1.1 国内汽车用紧固件现状
图1为世界紧固件应用行业分配比例图,从图中可以看出,电子工业、维修与建筑工业、汽车工业是紧固件
的三大用户。汽车工业所需的紧固件数量占紧固件总销量的23.2%,在三大用户中占有最大的比例,而维
修与建筑工业和电子工业分别位居二三位,占20%和16.6%。

汽车紧固件种类繁多,主要分为四大类,包括
标准紧固件、非标准紧固件、标准机械元件和非标准机械元件,其中非标准紧固件质量要求最高。非标准紧
固件中,如汽车发动机连杆螺栓、飞轮螺栓、车轮螺栓、悬挂螺栓等由于其要求很高的质量和良好的稳定性
,我国还不能达到国产化要求,大部分依赖进口。“十二五”整车期间,我国上海大众、上海通用、东风富康、广州本田、奇瑞、吉利、力帆、比亚迪等在内的整车企业迅速发展,必将在今后的一段时间内带动汽
车紧固件的迅速发展。
2013年,我国汽车销量突破2000万辆,而在汽车工业中,轿车的需求量是最大的,而轿车中紧固件的需求量
也随之增加,对于轿车紧固件来说,质量要求十分严格,其杆类紧固件和螺母类紧固件的强度要求大部分在
8级以上,产品结构也发生较大的变化。以乘用车为例,我国引进的高档的品牌汽车占80%以上,这些高档
品牌汽车虽然在国内生产线上装配,但车上所用紧固件大部分还是直接从国外引进,乘用车所用的紧固件原
料主要包括低碳钢线材和不锈钢线材,由这些原料制成的紧固件其强度大,而对于一些强度要求在10级以上
的异型紧固件,则需由定点专业的配套工厂生产,我国在制造这些高强度紧固件的原料和紧固件产品在质量
稳定性方面都存在问题。
据统计,一辆中型商用车所用紧固件数量达到两千多个,加上其它的连接附件,其总耗材质量多达100kg;
商用车的汽车发动机所用紧固件强度要求达到10级以上,而其它部位紧固件强度则要求达到8级以上。
我国汽车行业对紧固件重视不足,导致汽车紧固件的发展远远滞后于汽车行业的发展。
针对我国汽车紧固件行业的发展现状,可以从两个方面进一步提高:一方面,提高自主创新能力,掌握原创
性和自主知识产权,而我国汽车紧固件大部分研发模仿国外产品;另一方面,改进生产装备,提高产品质量
稳定性,而目前国内企业主要采用人工挑选,缺陷标准控制在(150~200)×10-6,而国外水平
控制在(60~90)×10-6。我国的材料和装备和国外的先进水平还
存在一些差距,我国在专业材料和专业技术方面还有待提高。
1.2 汽车用紧固件的安全性
紧固件在汽车成品中所占比例小,但对于整车造成的损害却是很大的,从发生事故的汽车来看,由于紧固件
损坏造成的事故达一半以上,有的甚至危及人的生命安全,而追究紧固件损坏的原因,主要取决于紧固件所
用材料的好坏。
1.2.1 失效形式
紧固件在各类机械零件或者建筑结构件中,主要起到连接的作用,当外界对结构件施加载荷的时侯,紧固件
能够使结构件保持原有的连接状态而不产生失效预紧载荷。由于结构件所承受载荷的形式多变,如、工作载
荷和冲击载荷,紧固件会在这些载而将荷的作用下产生失效,主要有断裂和松脱。结构件中任何一个紧固件
连接点的断裂和松脱,会引起整个结构连接链的失效,其中断裂会造成结构连接件的断开。紧固件发生断裂
的原因可以从以下三个方面进行分析,紧固件所用材料强度不够,在外界载荷的作用下发生断裂;由于紧固
件所用材料在热处理过程中不合理,存在表面裂纹等缺陷;由于紧固件在外界长期载荷作用下产生疲劳断裂
。
1.2.2 性能及组织要求
高质量紧固件所用的钢在性能上需要达到以下要求:1)紧固件所用的钢原料在塑性变形中具有较高的伸长率
和断面收缩率;2)紧固件在冷塑性变形中,所用钢材料具较小的变形抗力,在加工变形过程中硬化率低,具
有较小的屈强比值。高质量的紧固件所用钢在组织上需要达到以下要求:1)紧固件所用钢的显微组织主要由
铁素体加珠光体组成,其中铁素体所占比例达到60%以上,剩余为珠光体;2)紧固件所用钢中所含的非金属夹杂物,氧化铝和球状氧化物大小级别应小于0.5级,所含夹杂物总和应小于3级;3)紧固件所用钢表面不存在表面裂纹等缺陷,如凹凸折叠、结疤、麻点等,否则紧固件在冷镦过程中容易造成开裂的危险。
1.2.3 改进方向
为了生产出高质量的紧固件产品,在选用紧固件所用钢的过程中,必须严格控制所用钢的化学成分,减少钢
中有害元素S、P、O的含量,减少氧化物、硫化物夹杂对紧固件生产过程中产生开裂的影响;在冶炼和轧制
的过程中,通过控制工艺参数,如降低压下量、减少轧制次数和翻钢次数,使紧固件所用钢在生产过程中减
少折叠,获得均匀、细小的晶粒组织。在生产紧固件产品的过程中,先进的生产设备是保证高质量紧固件的
前提,正确的选用轧辊和变形均匀的孔形系统,有助于提高成品的合格率,保证产品表面的光洁;在紧固件
热处理过程中,严格控制加热炉内的温度、时问和气氛,降低紧固件成品表面的烧损和脱碳;加强钢坯在整
个生产过程中的质量检测,避免钢坯表面存在裂纹等缺陷。
为了保证紧固件大批量的生产需求,紧固件生产者需要保证紧固件的高质量和高稳定性。尽管生产者对关键
生产工序进行了严格的控制,但仍然不能保证生产出完全的好产品,产品合格率无法提高。因此,在生产完
成后必须进行最终的分选和检测,如人工挑选、涡流分选、光学传感尺寸及轮廓分选,分选出具有明显缺陷
的不良产品,如存在表面裂纹、表面脱碳和尺寸不合格的产品,以满足客户的要求。无缺陷的紧固件是保证
汽车装配线的顺畅运行、车辆的安全行驶以及厂家的良好声誉的关键所在。因此,近年来国外紧固件企业大
量涌人国内,而我国的紧固件企业挑战和机遇并存。国内紧固件企业需要打造品牌、提高品质、确保更高的
零件合格率,向零缺陷的目标不断努力。
2、紧固件行业热处理技术
随着汽车产业的发展,节能、环保、轻量化、小型化、薄壁化的要求不断增长,而汽车用紧固件越来越受到
重视。用于制造汽车紧固件的钢材需具备良好的强度和塑性,经热处理后可获得预期的综合性能,且资源丰
富价格相对较低,并具有一定的可利用再生性,较其他材料具有更高的性价比。热处理工艺是汽车紧固件用
钢获得良好综合性能的关键之一,不合理的热处理工艺会直接导致紧固件的失效。
2.1 紧固件行业热处理概况
紧固件所用钢材都要经过不同工艺的热处理,达到紧固件力学性能的要求。根据紧固件所用钢材的力学性能
要求和热处理工序的前后顺序,将热处理分为三步,第一步为钢材的热处理,包括软化退火和球化退火;第
二步为中问热处理,包括再结晶退火和低温退火;第三步为紧固件成品的热处理,为调质处理。
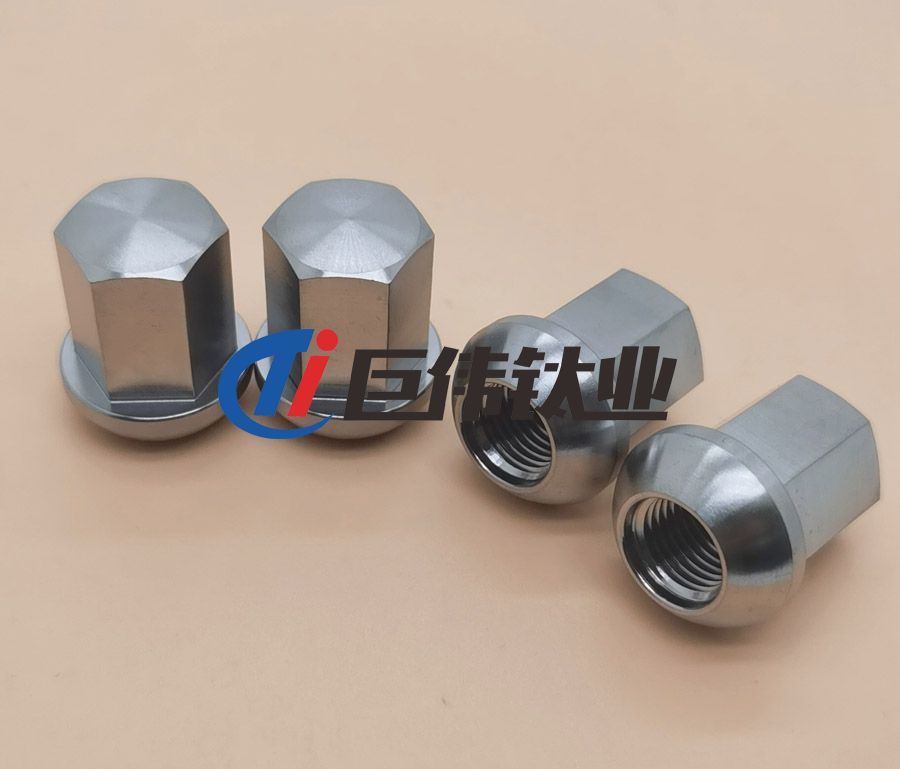
据统计,到2007年底,我国共有紧固件企业七千余家,年产量达到520多万吨,其中8级以上的紧固件产量约
220万吨,需要热处理的高强度紧固件高达40%。我国生产紧固件企业中共有热处理设备2700多台,其中可
控气氛连续式加热网带炉1600多台。紧固件成品的调质处理采用连续式网带炉,紧固件的平均热处理价格约
725元/t,每年的紧固件的加工收入约15.5亿元。按紧固件热处理的电费成本占年加工收入的70%推算,热
处理的电费成本约10.85亿元,按全国平均电费价格0.7元/kw推算,紧固件的年耗电量约15.
5×109kW·h,紧固件的平均加工耗能约775kW·h/t,而欧美国家的紧固件的平均加工耗能约
425kW·h/t,仅为国内紧固件的平均加工耗能的一半。紧固件热处理辅料,如热处理用各类淬火介质、发
黑剂、清洗剂,每年消耗量计1500余万元;紧固件热处理配件,如耐热钢备件、工装夹具等,每年消耗量计
700余万元;平均利润率在12.5%左右。
2.2 紧固件热处理的技术
为了获得高质量的汽车紧固件,紧固件在调质热处理的过程中,必须采用先进的热处理装备和先进的生产技
术,保证热处理的顺利进行,从而使紧固件获得较高的抗拉强度和屈服强度比。调质热处理工艺主要包括加
热、淬火和回火三个步骤,其中加热和回火前均需对原料进行彻底的清洗,整个步骤完成后即可进行着色后
下线。比如东风汽车的紧固件,通过调质热处理需要达到四个强度级别的紧固件:8.8级、9.8级、10.9级和12.9级,而在热处理过程中,原材料材质、热处理调质炉温度、炉内气氛、淬火介质、成品后的质量检测等都是影响紧固件质量的关键因素。
2.2.1 材料材质
国内紧固件所用钢在使用过程中存在偏析、脱碳、裂纹等问题,这主要是由于两方面因素引起的,一方面紧
固件所用钢的原料在冷成型前没有进行球化退火;另一方面退火过程中退火炉没有采用气氛保护,使钢原料
的表面脱碳。而国外一些企业从材料和退火保护气氛两方面人手,很好地解决了钢原料的脱碳问题。日本神
户企业采用球化钢作为紧固件所用钢原料,紧固件生产厂家不需要对钢原料进行球化退火,因此也不存在脱
碳的问题;俄罗斯的紧固件企业对钢原料进行感应加热,然后再在保护气氛下进行球化退火,该工艺很好地
解决了紧固件钢原料的脱碳问题。
2.2.2 热处理调质炉
国外的热处理调质线广泛采用铸链式和网带式,这两种调质线在炉子密封性、计算机控制和故障显示等方面
具有明显的优势。高强度紧固件从加热、淬火和回火,其中包括加热和回火前的清洗工序,整个步骤完成后
的着色和下线,均由计算机全程自动控制运行,可以有效保证材料热处理质量的稳定性。
国内企业大部分自动化程度不高,以东风汽车的8.8级的高强度紧固件为例,其调质处理在震底炉上进行,
受到热处理炉设备条件的限制,该炉子密闭性差,保护气氛纯度不易控制,炉温温差大,且零件实际的加热
时间不确定,零件在炉内加热过程中存在碰撞摩擦的现象,因此会存在材料表面脱碳、局部加热不均、零件
相互碰伤等现象。
2.2.3 淬火介质
调质热处理后进行淬火所用的介质对于热处理来说起着非常重要的作用,它直接影响紧固件所用钢原料热处
理后的冷却能力,会直接导致淬火开裂和变形等现象。国外高强度紧固件在进行调质热处理后,对中碳钢采
用水溶性淬火介质(PVG)或快速淬火油进行淬火。而国内紧固件企业大部分采用两种淬火介质:碱水和普通
机械油。在碱水中淬火,紧固件表面容易产生淬火开裂的现象,而在普通机械油中淬火,紧固件表面存在硬
度不均的现象,因此在实际生产中不得不对紧固件钢原料反复进行调质热处理。
2.2.4 检测
为了保证紧固件质量的绝对可靠,完善的检测设备是质量保证必备条件,国外采用直读光谱仪对紧固件钢原
料的化学成分进行快速检测;并对原料是否存裂纹等缺陷进行在线无损检测,以保证原材料在进人热处理前
处于完好状态;紧固件在进行调质热处理时,采用碳势控制、温度控制和工艺参数的控制;淬火介质实行温
度和冷却速度的监测,淬、回火后硬度测量和金相测定。必要时进行定量测定,对调质后零件进行荧光磁粉无损探伤、零件内在缺陷分选和强度、硬度等力学性能的测定。
而国内企业的热处理后的紧固件主要进行硬度、抗拉强度、金相组织的检测和保护气氛分析,仅部分高级别
紧固件进行磁粉荧光无损检查零件内部裂纹等缺陷。而淬火介质冷却温度和冷却速度的测定、金相组织的定
量分析等却达不到检测要求。
2.3 紧固件热处理设备的更新
我国政府大力倡导建设资源节约型社会,提出了3年内节约能耗20%的硬性指标,鼓励企业必须进行技术改
造和设备更新。而且随着紧固件行业竞争的日趋激烈,客户对紧固件产品质量,诸如轻量化、环保、长寿命
等方面的要求不断提高,企业的设备将会不断改造更新,先进热处理装备的投入在相当长的一段时间里仍将拥有较大的发展空间,以适应国外国内市场的发展和需要。
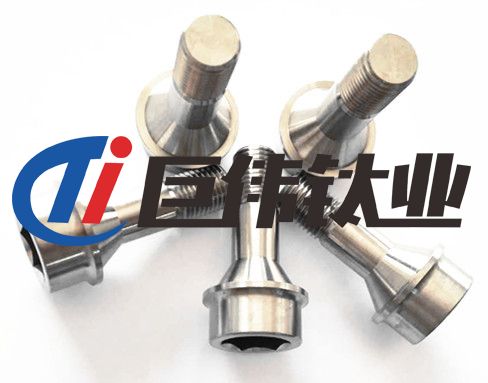
紧固件企业热处理设备的改造和更新主要趋向使用可控气氛网带炉和多用炉,来代替传统的井式炉和网带炉。与电加热炉相比,燃气加热炉具有更高的加热效率。采用电加热方式加热,热能的利用率仅为30%左右
;而采用燃气加热方式加热,热能的利用率可达到60%左右。连续式网带炉生产线的加热区采用燃气加热,
保温区采用电加热,能够充分发挥燃气加热和电加热的优势,在我国天然气资源丰富的地区,这一技术将得到广泛的推广和应用。
密封箱式多用炉工艺灵活,能对长杆类紧固件进行淬火处理,工作温度可提高到1050~1100℃,具有高效、
节能、低成本和清洁生产的特点,是中小型紧固件企业技术改造与设备更新的适用炉型。
3、结语
国内汽车紧固件企业虽然与国外先进水平相比还存在明显差距,但是我国紧固件企业经过长期的发展,具备
了一定的产业基础和优势。随着汽车行业的市场竞争日趋激烈,汽车紧固件轻量化、环保、长寿命等方面的
要求不断提高。我国作为全球汽车产销第一大国,汽车紧固件企业不断快速发展与壮大。从世界格局来看,
我国紧固件行业无论是横向规模发展还是纵向技术升级都具有广阔的发展空间,汽车紧固件的发展和振兴之
路任重道远。
参考文献
[1]冯琴.我国汽车紧固件产业现状和展望[J].现代零部件,2013(2):61—63.
[2]王卫芳.浅谈紧固件热处理的质量管理[J].热处理技术与装备,2015,36(2):59—62.
[3]刘金霞.我国的汽车召回制度浅析[J].重庆科技学院学报:社会科学版,2010(19):104—105.
[4]金荣植.汽轮机紧固件淬火裂纹分析及改进措施[J].热处理技术与装备,2010,31(1):23—27.
[5]冯琴.浅述大陆冷镦钢的生产和发展[J].螺丝世界,2008,112:84—85.
[6]何吉林,孙建明.持续改进产品质量是制品企业生存发展的保证[J].金属制品,2008(5):54—56.
[7]侯维明,徐云峰.高强度紧固件断裂原因分析[J].金属制品,2010(5):80—13.
[8]张先鸣.汽车高强度紧固件热处理工艺[J].现代零部件,2012(8):42—44.
[9]祝其高,张先鸣.我国紧固件行业技术发展[J].金属制品,2010(1):11—13.
[10]吴光治.热处理的节能减排[J].热处理技术与装备,2008,29(3):5—8.
[11]张先鸣.风电机组上紧固件用的B7钢材料[J].热处理技术与装备,2010,31(2):15—18.
相关链接