1、引言
航空航天制造业作为高新技术密集型产业,一直代表着世界各国制造业的发展方向,是一个国家制造业实力和国防工业现代化水平的综合体现;而航空航天高端装备的服役性能在很大程度上取决于构件的性能。航空航天高性能构件多服役于极端严苛环境中,具有超强承载、极端耐热、超轻量化和高可靠性等特性,对构件的材料、结构、工艺和性能等提出了严峻挑战。近年来,增材制造技术(亦称3D打印技术)正成为工程、制造、材料、光学等学科的研究热点,基于增材制造技术可实现复杂结构金属构件的材料-结构一体化净成形,为航空航天高性能构件的设计与制造提供了新的工艺技术途径。增材制造(3D打印)全球权威发展报告“WohlerSReport”指出,航空航天是增材制造技术研发与工业应用最有望获得突破的领域,增材制造已发展成为提升航空航天设计与制造能力的一项关键核心技术,其应用范围已从零部件级(飞机、卫星、高超飞行器、载人飞船的零部件打印)发展至整机级(发动机、无人机、微/纳卫星整机打印)。增材制造技术在航空航天领域的应用主要得益于其在轻量化高性能材料及结构一体化成形领域取得的显著效益。

增材制造是国内外科技强国竞相发展的一项关键核心技术,国家自然科学基金委员会(NSFC)、美国科学基金会(NSF)(2010)将增材制造认定为20世纪制造技术的一项重大创新。“美国制造:国家增材制造创新研究院(NAMII)”(2013年)、《德国工业4.0战略计划实施建议》(2013年)将增材制造技术作为新一代革命性技术以及未来科研和产业发展的新增长点而加以培育和支持。中国政府在《中国制造2025》(2015年)、《国家增材制造产业发展推进计划(2015—2016年)》(2015年)、《国务院关于印发“十三五”国家战略性新兴产业发展规划的通知》(2016年)、《加强“从0到1”基础研究工作方案》(2020年)等科技强国和制造强国战略行动纲领中,前瞻性地布局了增材制造关键核心技术,打造及完善增材制造产业链,力求占领技术发展战略高地。
基于激光技术实现高熔点难加工金属、合金及金属基复合材料构件的直接成形,是增材制造技术研发领域最为热门的方向之一;而基于激光与粉末的增材制造技术已形成两类典型成形工艺,并表现出两种不同的发展方向:一类是基于喷嘴自动送粉的激光熔化沉积(LMD)技术或激光立体成形(LSF)技术,它利用高能激光熔化同步供给的金属粉末,采用特制的喷嘴在基板上逐层沉积成形构件。LMD沉积层厚度为毫米尺度,制造速度快,适合制造大型构件,这是该技术应用及发展的主要方向。此外,LMD成形件通常需要进行后续精整加工,以达到结构控形及尺寸精度的要求。另一类是基于粉床自动铺粉的选区激光熔化(SLM)技术或激光粉床熔融(LPBF)技术,它利用高能激光熔化处于松散状态的粉末薄层(厚度通常为20~50μm),基于粉床逐层精细铺粉、激光逐层熔凝堆积的方式,成形任意复杂形状的高致密度构件。SLM技术成形精度高,对特殊复杂结构(如悬垂结构、薄壁结构、复杂曲面、空间点阵等)制造的适用程度高,其发展方向是实现中小型复杂构件直接精密净成形。不论是面向大型金属构件的LMD技术,还是面向中小型精密金属构件的SLM技术,均为高性能复杂结构金属构件的低成本、短周期、净成形制造提供了一体化解决方案,在航空航天等领域具有广阔的应用及发展前景。对比金属激光增材制造技术的国内外发展历程及现状可知,德国、美国等国在激光增材制造的原创性工艺技术、核心光学部件(如激光器、振镜等)、高性能金属粉末材料上有较深厚的研发积累,而我国的金属激光增材制造技术发展水平近年来显著提升,金属增材制造装备、材料、工艺、软件等朝着国产化、产品化、专业化方向不断推进,特别是在航空航天重大需求的牵引下,高性能大尺寸金属构件激光增材制造的工艺研发及应用水平已走在了国际前列。近年来,在国家航空航天重大需求和前沿科学探索的双重驱动下,金属构件激光增材制造研究在材料、结构、工艺、技术、性能/功能等多方面呈创新发展之势。从航空航天领域日益增强的工程需求出发,面向极端严苛环境的航空航天构件的服役性能要求不断提升,故要求构件的强度、韧性、刚度等力学性能指标显著提高,并要求构件具有防热、隔热、减振、抗辐射等特殊功能。只有通过创新发展增材制造的新材料、新结构、新工艺,才能有望获取颠覆性的性能和功能,满足国家航空航天领域重大工程的需求。基于前沿科学探索与发展角度,发表于Sciencs的《金属的未来》(2011年)一文指出:现代工业要求结构材料具有高的强度、断裂韧性及刚度,同时尽可能减重,即要求材料的比强度更高;在提高材料比强度的同时,不损害其韧性和塑性等性能,对提高材料的工程应用竞争力至关重要。同时,Sciencs论文预测指出,多材料(如具有可控增强结构的金属基复合材料)是解决传统金属材料比强度和比刚度低、耐蚀性差等劣势的重要途径。与前沿科学探索相一致,随着现代航空航天工业的快速发展,以铝、钛合金为代表的轻质高强合金、以Ni基高温合金为代表的承载耐热合金,是各国新材料研发计划中重点发展的材料之一,也是激光增材制造中重要的应用材料。现代航空航天构件需同时满足轻量化、高性能、高可靠性、低成本等一系列苛刻要求,且构件的结构更为复杂、设计制造难度更大。通过创新和发展航空航天典型铝、钛、镍基构件激光增材制造控形与控性关键技术,既体现了选材上轻量化、高性能的发展方向,又凸显了增材制造技术本身精密化、净成形的发展趋势,可实现材料-结构-性能的一体化增材制造以及增材制造技术在航空航天上的重大工程应用。
本文针对航空航天领域三类典型应用材料(即铝、钛、镍基合金及其金属基复合材料)、四类典型结构(大型金属结构、复杂整体结构、轻量化点阵结构、多功能仿生结构等),阐述了近年来国内外在面向激光增材制造的新材料制备、新结构设计、成形件控形与控性、高性能/多功能突破、航空航天领域典型应用等方面的研究进展,提出了高性能金属构件激光增材制造的宏/微观跨尺度形性协调机制,并就激光增材制造技术未来在材料、结构、工艺、性能等方面潜在的研究方向作一点思考与展望。
2、面向激光增材制造的高性能金属材料
2.1激光增材制造铝合金及铝基复合材料
对于激光增材制造而言,铝基材料是典型的难加工材料,这是由其特殊的物理性质(低密度、低激光吸收率、高热导率及易氧化等)决定的。从增材制造成形工艺角度看,铝合金的密度较小,粉体流动性相对较差,在SLM成形粉床上铺放的均匀性较差或在LMD过程中粉末输运的连续性较差,故对激光增材制造装备中铺粉/送粉系统的精度及准确性要求较高。未熔化前,铝对CO2激光的初始吸收率仅为9%,而其热导率高达237W/(m·K),为铁的3倍、钛的16倍,通常的低功率CO2激光难以使铝粉体发生有效熔化。即便使用短波长、高功率光纤或Nd∶YAG激光使铝粉发生初始熔化,其高的热导率又将使输入热量急速传递而消耗掉,导致熔池温度降低、熔池内液相的黏度增加;同时,高温下铝熔体与氧具有很强的亲和力,而激光成形腔体内即便通过抽真空或通保护气体使氧含量降至10×10-6(体积分数)以下,系统内残余的氧元素也会在熔体表面形成氧化膜,降低熔体的润湿性和铺展性,进而将促进金属粉末SLM增材制造特有冶金缺陷-----“球化”效应及成形件内部孔隙、裂纹等的发生,从而显著降低激光增材制造构件的成形性能。
相对于钛基、镍基等金属材料对SLM和LMD两种工艺表现出的广泛适用性,铝基材料激光增材制造的研究工作及应用验证较多集中在SLM工艺上。目前基于SLM成形的铝合金及铝基复合材料如表1所示。其中,AlSi10Mg和AlSi12等Al-Si合金具有良好的铸造性能和焊接性能,故对SLM这类经历粉末熔化/凝固冶金热物理过程的增材制造工艺表现出了良好的成形性能。激光增材制造Al-Si系合金的显微组织演变规律和调控机制较为一致:在激光非平衡快速凝固条件下,SLM成形AlSi12呈现为微细的富铝胞状组织,残余硅颗粒在晶界析出;经热处理后,显微组织将发生一定程度的粗化,硅组元从晶胞中继续析出并形成硅颗粒。SLM成形AlSi10Mg表现出与AlSi12相似的显微组织特征及演变规律。需要指出的是,析出硬化AlSi10Mg合金在SLM激光快速凝固过程中并没有析出Mg2Si沉淀相,但细化的亚微米胞状组织仍为激光成形件提供了较高的强度。激光增材制造工艺参数(如激光光斑尺寸、激光功率、扫描速度、扫描间距、铺粉厚度等)及扫描策略、成形方向、成形件布局方式等均可显著影响构件的成形质量、显微组织及最终的力学性能。为综合评估SLM诸多工艺参数的耦合作用,可通过“激光线能量密度”(λ=P/v)综合“激光功率P”和“扫描速率v”的影响,且可通过“激光体能量密度”(ε=P/(vhd))进一步耦合“扫描间距h”和“铺粉厚度d”的影响,分别用以调控“线成形质量”和“体成形质量”,为金属构件SLM激光增材制造的精确化、稳定化控制提供关键工艺参数指标,并为激光成形件内部显微组织、冶金缺陷、残余应力及成形性能的“由线及体”的立体控制提供关键方法及科学机理。AttAllah小组研究了SLM工艺参数对AlSi10Mg致密化行为的影响规律,发现采用较高的激光功率、较低的激光扫描速度和较小的扫描间距可有效减少或消除成形件内部的孔隙,且AlSi10Mg合金获得良好SLM成形性能所需的体能量密度阈值在60~75J/mm3之间。ThijS等[24]学者在SLM激光扫描策略优化的研究中发现:当采用岛状扫描策略进行SLM成形时,Al-Si合金的晶体织构明显减弱,沿着成形方向形成较弱的〈100〉立方织构,成形件各方向的拉伸强度主要受织构的影响,表现为各向同性;然而成形件的韧性却表现为各向异性,这是由于微观组织的各向异性使得裂纹通常沿着熔池边界形成,故平行于扫描方向的延伸率更高。减小扫描路径长度,可降低相邻熔道间的热量损耗,热量积累更均匀,温度梯度减小,可降低激光成形件的残余应力。Wang等研究了扫描策略对SLM成形AlSi10Mg力学性能的影响规律,发现岛状扫描成形试样的抗拉强度和延伸率高于相同工艺参数下线性扫描成形试样。
表1激光增材制造铝合金及其复合材料的力学性能
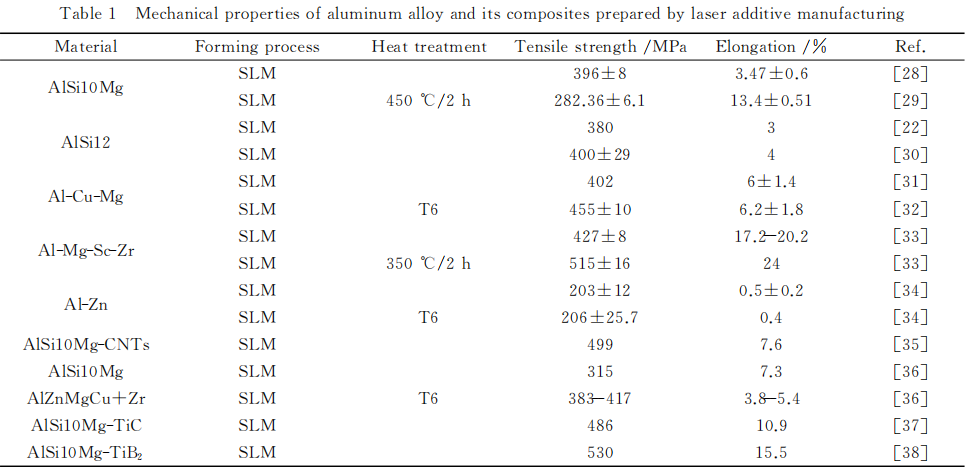
如表1所示,Al-Si系合金因其铸造铝合金的材料本质,虽然采用经过优化的激光增材制造工艺进行制备,但抗拉强度很难突破400Mpa,从而限制了其在航空航天等领域服役性能要求更高的承力构件上的使用。为进一步获得更高的力学性能,近年来Al-Cu、Al-Mg和Al-Zn等铝合金体系也被用作SLM成形材料,但这类铝合金中较高的合金元素含量和较宽的冷却凝固温度范围,使得沉淀强化合金在激光增材制造过程中易形成裂纹甚至发生开裂;且相对于铝元素,镁和锂等合金元素更易在高能激光的高温作用下发生气化蒸发,从而影响成形件的成分稳定性及力学性能。Zhu研究小组发现:激光体能量密度对Al-Cu-Mg(2024铝合金)SLM致密化行为具有显著影响,当激光体能量密度高于340J/mm3这一阈值时,可获得无缺陷、无裂纹的高致密度(相对密度为99.8%)成形件。激光成形显微组织由微细过饱和的胞状晶-树枝晶复合结构组成,在细晶强化机制和固溶强化机制的协同作用下,成形件的抗拉强度可达402Mpa,屈服强度可达276Mpa。2024铝合金等高强铝合金较难通过激光增材制造工艺获得预期的高性能,这主要是由于该材料的成分和物性参数并非是专门为激光增材制造设计的。因此,对于激光增材制造高强铝合金而言,成分、物性参数、相变的设计及调控尤为重要。近年来,人们设计了专用面向激光增材制造的稀土元素钪改性增强的Al-Mg-Sc-Zr合金粉末,其激光成形件的力学性能有望获得突破性提升。SLM成形Al-Mg-Sc-Zr合金直接沉积态试件的组织呈典型的双峰晶粒分布:在熔池边界处,以初生Al3(Sc,Zr)相和细小的Al-Mg氧化物作为形核点,形成等轴晶区;在熔池中部形成沿温度梯度生长的柱状晶区。激光增材制造Al-Mg-Sc-Zr合金力学性能的跃升需辅以适当的后续热处理工艺。经325℃/4h时效处理后,SLM成形Al-Mg-Sc-Zr合金中的晶粒无明显粗化现象,其基体内可原位析出尺寸为5~10nm的二次Al3(Sc,Zr)相,该析出相与基体保持共格界面,可有效钉扎位错,具有显著的纳米弥散强化效应,可显著提升成形件的综合力学性能(抗拉强度高于500Mpa,延伸率超过10%)。制备铝基复合材料是铝合金强韧化的重要途径。铝基复合材料兼具轻合金与陶瓷、纤维等增强体的优良特性,具有高的比强度、比模量及体积稳定性,并具有耐高温、抗磨损及抗氧化等优异的性能以及材料可设计性。激光增材制造铝基复合材料在选材上突出“多相材料可设计性”,在增材制造工艺上强调“高可控性”,在使用成效上则凸显“高性能/多功能”,这也代表了增材制造技术的重要发展方向。纳米陶瓷增强和原位陶瓷增强可有效改善陶瓷/金属界面的润湿性及结合性,抑制界面上的微观孔隙及裂纹,提升激光成形件的力学性能。笔者研究团队基于SLM过程中高能激光对纳米陶瓷微粒完全熔化及润湿的成形机制,实现了四类陶瓷(包括TiC、SiC碳化物,TiB2硼化物,AlN氮化物,Al2O3氧化物)、两类增强方式(包括纳米弥散增强和原位析出增强)的铝基复合材料的激光增材制造,发现了高能激光辐照特有的加热方式(具有逐点逐行区域化扫描特征)、能量特点(瞬态升温可达5000°C以上)及冶金机制(激光快速凝固速率高达106K/S)可使铝基复合材料的纳米/原位陶瓷增强相具有环状、条带状、层片状等新颖的微观结构(如图1(a)、(b)所示),这些新颖的微观结构显著区别于传统铸造或粉末冶金铝基复合材料的颗粒状增强结构;揭示了激光增材制造过程中高度非平衡熔池内的Marangoni流、温度场、速度场、溶质场等冶金热力学和动力学行为对纳米/原位陶瓷增强相形成、晶体生长和空间分布起决定性作用;发现了激光作用下形成的具有独特显微组织及分布的纳米/原位陶瓷增强相与铝基体间具有共格界面且两相原子匹配性强,在纳米/原位陶瓷增强相的作用下,铝基体可发生显著的等轴晶化及晶粒细化(如图1(c)所示),基于增强相与基体相的显微组织调控可使激光增材制造铝基复合材料构件的强度和断裂韧性获得协同提升。
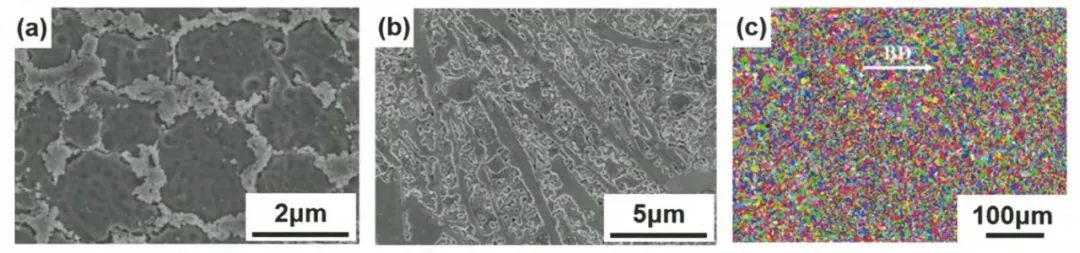
图1激光增材制造铝基纳米/原位复合材料的显微组织调控。(a)环状TiC纳米增强相;(b)条带状Al4SiC4原位增强相;(c)TiB2增强作用下铝基体细化的等轴晶组织
对于不可焊6系和7系铝合金等激光增材制造裂纹敏感性特别强的材料,纳米颗粒改性和增强的策略是显微组织改善的良策,可改善激光增材制造试件的成形性能和力学性能。对于6系和7系铝合金来说,在SLM激光快速凝固过程中,溶质易在凝固界面附近的熔体中偏析,引起显著的成分过冷,凝固组织易呈树枝状晶长大,并在凝固组织间形成较长的液相通道;当凝固温度进一步降低时,液相凝固收缩产生孔隙、裂纹甚至热撕裂。MarTin等学者在Nature上发文指出,他们通过纳米颗粒改性增强的策略解决了上述问题;他们根据结晶学信息选择纳米锆粒子作为成核剂,然后通过静电附着将其组装到7075和6061系铝合金粉末颗粒表面,最后采用SLM技术成形。他们发现,在激光熔池中锆颗粒与铝基体发生反应生成的Al3Zr,提供了大量低能量势垒非均质形核位点,促进了微细等轴晶的形成,从而降低了凝固收缩应力的影响,获得了具有均匀等轴晶组织、无裂纹且强度高的铝基构件,如图2所示。此外,航空航天等极端严苛的服役环境对铝合金构件的强度、韧性、模量、刚度等性能指标提出了严格要求,因此,高体积分数的陶瓷增强铝基复合材料的制备具有重要的工程应用价值。NatureCommunicaTionS报道了Lin等学者在制备纳米TiC增强铝基复合材料方面的工作,他们首先制备了具有高体积分数(最高可达35%)的纳米TiC增强铝基纳米复合粉末,然后利用SLM工艺实现了块体铝基复合材料的制备,成形件的屈服强度高达1000Mpa,塑性超过10%,杨氏模量约为200GPa,这是目前结构金属材料中比杨氏模量、比屈服强度最高的材料;这些性能的提升主要归因于高密度分散的纳米增强颗粒、纳米颗粒与铝基体间的强界面结合以及激光作用下形成的超细晶粒。
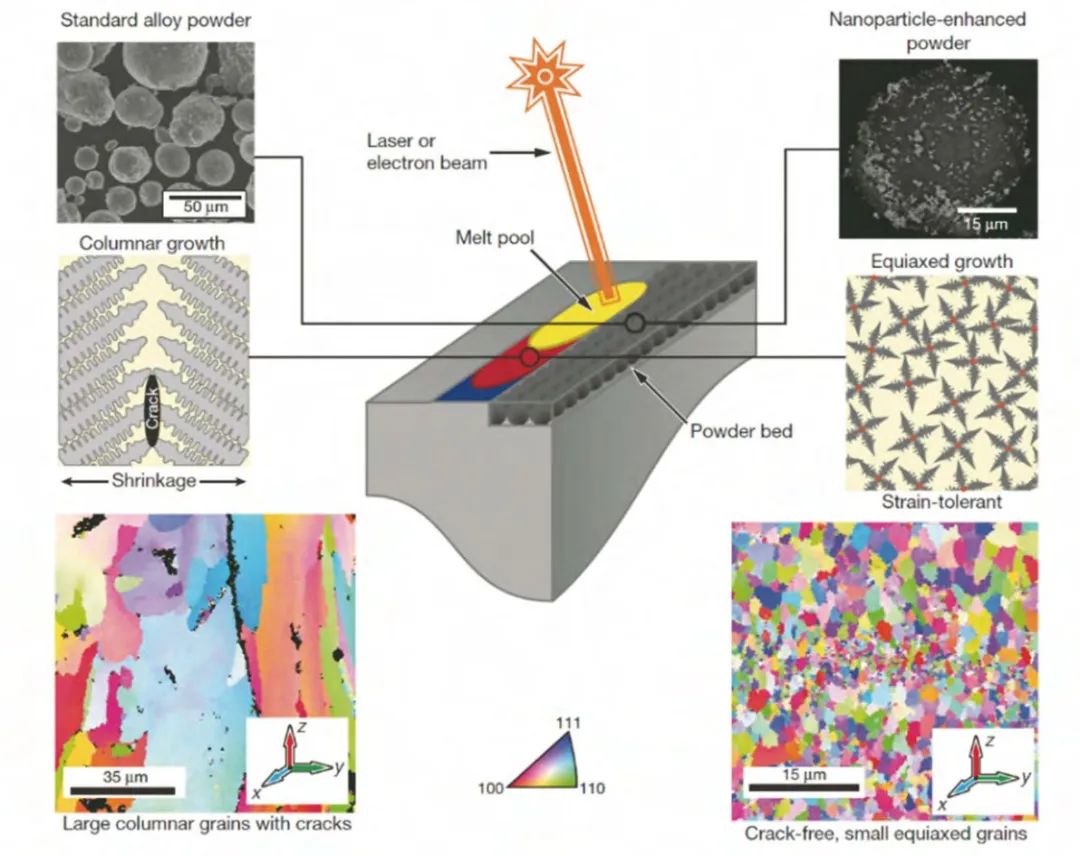
图27075铝合金的SLM增材制造:基于纳米颗粒改性实现柱状树枝晶向微细等轴晶转变及裂纹抑制
2.2激光增材制造钛合金及钛基复合材料
钛基材料因具有优异的比强度、耐蚀性和生物相容性而被广泛应用于航空航天、生物医疗、食品化工等领域,是激光增材制造经常采用的金属材料。目前激光增材制造钛基合金的挑战在于:1)激光增材制造成形完全致密的复杂结构钛基构件尚存在难度,成形过程中构件易产生气孔、裂纹及表面球化等加工缺陷,这些加工缺陷往往会成为绝热剪切带和裂纹萌生源,降低成形件的力学性能和服役性能。2)激光增材制造过程中极大的冷却速度(103~108K/S)和温度梯度将诱发马氏体相变,使构件内部产生较大的残余应力;随着加工层数增加,残余应力逐渐增大,从而导致热裂纹形成,并且成形件易发生翘曲,这种加工缺陷积累至一定程度时会导致成形件发生开裂,并严重降低零件的塑性和韧性。3)在激光加工过程中,热流主要沿着平行于增材制造的方向传导,导致体心立方(BCC)结构的初生β-Ti相沿散热方向〈001〉β择优生长,并具有很强的外延生长倾向,易形成粗大的柱状晶组织,从而导致构件的显微组织和力学性能具有很强的各向异性。
钛基材料对SLM和LMD两类激光增材制造工艺均表现出了较强的适用性。目前用于激光增材制造的钛合金主要集中在工业纯钛(CP-Ti)及TC4等传统钛基材料上。激光增材制造构件的显微组织调控是其力学性能提升的基础,且与激光工艺参数密切相关。基于SLM工艺成形CP-Ti时,若采用较低的激光线能量密度,熔池熔体在凝固过程中会发生β-Ti向α-Ti的转变,从而导致组织呈较为粗大的板条状结构;随着激光线能量密度增加,熔池凝固过程中较大的过冷度导致β-Ti向马氏体α′-Ti发生转变,此时成形组织呈显著细化的针状结构。SLM成形TC4构件的显微组织通常为细小的针状马氏体。在增材制造方向上,初生β-Ti晶粒以柱状晶外延生长,柱状晶的长度可达100μm,远大于SLM每层的铺粉厚度(通常设为30μm);柱状晶的宽度与熔道宽度相当,随着激光能量密度的增加,熔道宽度增大,导致柱状初生β-Ti晶粒粗化。Xu等学者发现,通过优化增材制造工艺参数,可将SLM过程中形成的脆性马氏体相α′-Ti转化成具有更高韧性的(α+β)-Ti组织,从而可以省去后续的热处理。当增材制造层厚设为30μm时,熔池内部较大的温度梯度及冷却速度,使得凝固组织为马氏体α′-Ti;随着层厚增加至60μm或90μm,通过调控激光焦距可使α′-Ti发生分解,随后转变为细化的层状(α+β)-Ti组织,有效提升SLM成形TC4构件的综合力学性能。LMD成形的TC4构件通常表现出与SLM工艺成形构件相似的显微组织特征,凝固组织为柱状初生β-Ti晶粒。在凝固过程中,初生β-Ti晶粒沿增材制造方向穿过若干加工层发生外延生长,柱状晶的长度通常为1.5~10mm,同时在初生β-Ti柱状晶边界上可观察到α-Ti的晶界。通常情况下,LMD成形的TC4凝固组织不均匀:在靠近基板位置处,熔池的冷却速度较大,会生成较细小的层片状α-Ti组织及板条状α′-Ti马氏体组织;在构件顶部位置,冷却速度较小,凝固组织为α+β层状双相组织;构件中部位置因受到持续的热影响作用,铝元素及钒元素易向α-Ti及β-Ti内部偏析,导致成形组织不均匀,且晶粒较粗大,易产生加工缺陷。可见,激光增材制造虽涉及一系列复杂的工艺参数,但也为构件显微组织与力学性能的设计和调控提供了可能。表2所示为不同激光增材制造工艺及后处理工艺条件下钛合金的力学性能。可见,激光增材制造钛合金构件的力学性能与显微组织具有直接关系,而组织演变又受控于工艺,故高性能构件激光增材制造需要建立材料-组织-工艺-性能的一体化调控理论及方法。
表2激光增材制造钛及钛合金的力学性能
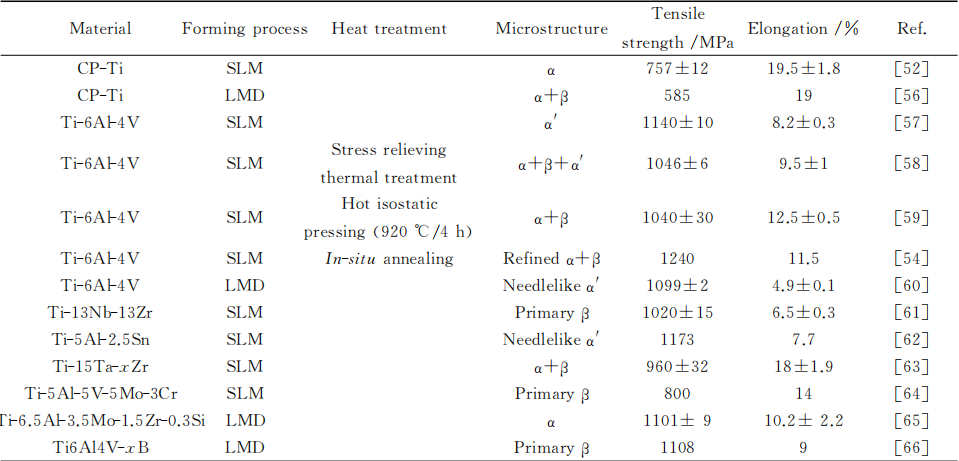
由于激光增材制造过程中熔池的冷却速度较快,且沿着增材制造方向具有较大的温度梯度,故而钛合金的凝固组织往往呈柱状晶结构,导致了成形件力学性能的各向异性。为改善钛合金激光增材制造过程中产生的各向异性,可从材料设计和工艺优化两方面加以改进。Nature报道了Zhang等学者研发的可用于激光增材制造的新型Ti-Cu合金,这类合金可在激光快速凝固过程中获得细小等轴的初生β-Ti晶粒,如图3(b)所示,且成形件内部没有明显的孔隙及裂纹,在增材制造方向上具有很高的化学成分均匀性。相比如图3(a)所示的激光增材制造TC4的凝固组织,Ti-8.5Cu合金中的初生β-Ti晶粒得到了显著细化,平均晶粒尺寸降至9.6μm。晶粒细化的主要原因是铜原子固溶在β-Ti基体中,显著扩大了凝固过程中固液前沿的成分过冷区,且随着铜在钛中的含量增加,晶粒细化效应更加显著。当铜的加入量为3.5%(质量分数)时,未经热处理的成形样具有较高的抗拉强度和延伸率,抗拉强度和延伸率分别为(867±8)Mpa和(14.9±1.9)%。NatureCommunicaTionS刊发了Barriobero-Vila等学者研发新型Ti-La合金的论文,该文阐明了α相稳定元素镧对钛合金相变过程及晶粒生长的作用机制。在钛中加入质量分数为2%的镧可使钛合金在凝固过程中发生包晶、包析及共析反应(L1+β→La-bcc,La-bcc+β→α,La-bcc→La-fcc+α),同时在固/液前沿产生了较大的成分过冷,促进了细小等轴晶的形成。通过包晶反应形成的α-Ti与原始β-Ti不具有严格的取向关系,可使Ti-La合金构件的各向异性显著降低。从激光增材制造金属构件的显微组织调控规律来看,晶粒的等轴化和均匀化有利于提升成形件的力学性能,而这也可通过在激光增材制造工艺中施加复合能场来实现。Qian研究小组通过在TC4构件LMD过程中复合20kHz的高频超声振动,使显微组织从柱状晶完全转变为粒径约为100μm的细小等轴晶,如图4所示。在复合能场辅助下成形的TC4构件的屈服强度和抗拉强度均比直接采用LMD成形的构件提高了约12%,且这种基于复合能场改善显微组织和力学性能的方法,对于Inconel625等镍基高温合金材料也同样适用。
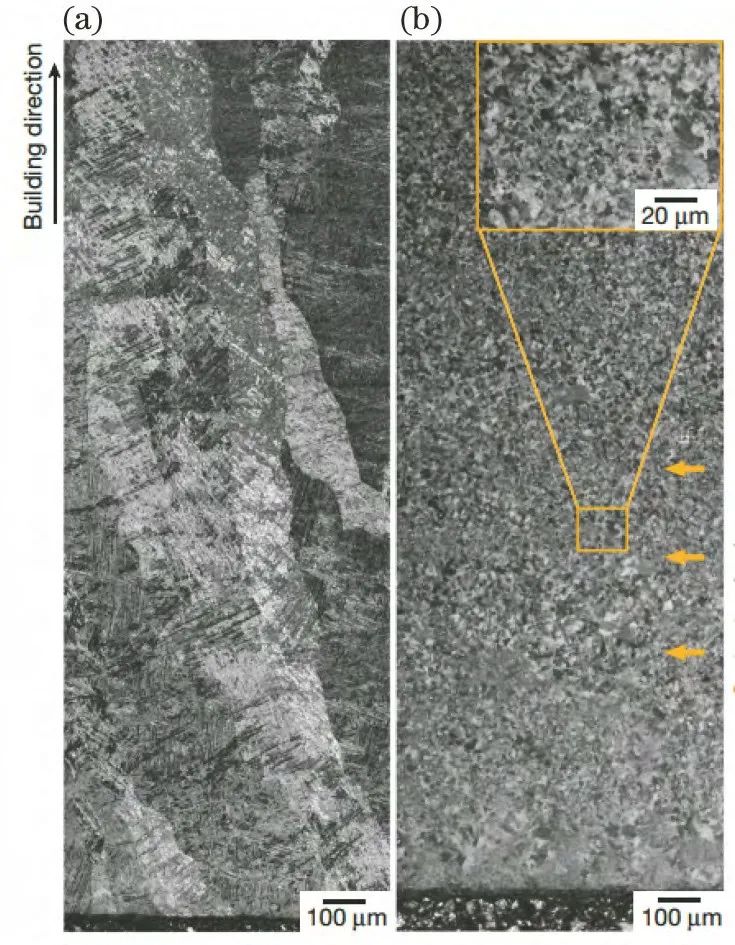
图3激光增材制造TC4合金与Ti-8.5Cu合金显微组织的对比。(a)TC4合金呈粗大的柱状晶组织;(b)Ti-8.5Cu合金呈细小的完全等轴晶组织
除了上述基于合金化的思路来研发激光增材制造新型钛合金外,制备陶瓷增强钛基复合材料也是提升钛基构件力学性能的重要手段。钛具有很强的化学活性,激光增材制造过程中钛组元易与其他组元发生原位化学反应,显著增大了激光成形材料物相和组织的调控难度,故对于钛基复合材料陶瓷增强相的选择上需慎重。在众多的陶瓷材料中,TiC及TiB2被认为是最适合用于钛基复合材料的陶瓷增强相。它们具有与钛合金相近的密度及热膨胀系数,且具有较高的物理化学稳定性,可与钛合金形成良好的物理化学兼容性。Liu等学者研究了LMD成形TiC-Ti6Al4V复合材料凝固组织与工艺参数之间的内在关系后发现:当激光功率为230W以及TiC陶瓷添加量为10%(体积分数)时,凝固组织中会出现初生球状TiC、共晶TiC及共晶球状TiC;随着激光功率增大,凝固组织中开始出现细小的初生枝晶TiC;随着激光功率进一步增至300W,这些初生枝晶长大,且数量增多。这种显微组织演变的主要原因是TiC增强相在不同激光功率下的熔化程度不同。随着激光功率增大,TiC增强相的熔化程度增大,更多的碳原子溶解在熔池中;当熔池中的碳原子含量增至一定程度时,初生枝晶TiC开始形成并附着在初生球状TiC上。初生TiC的产生需要消耗一定的碳原子,导致凝固组织中共晶碳化物的含量降低。不同形态的TiC与钛基体的结合能力不同,从而导致了不同的力学性能。当加入15%(体积分数)的TiC时,LMD成形TiC-Ti复合材料的抗压
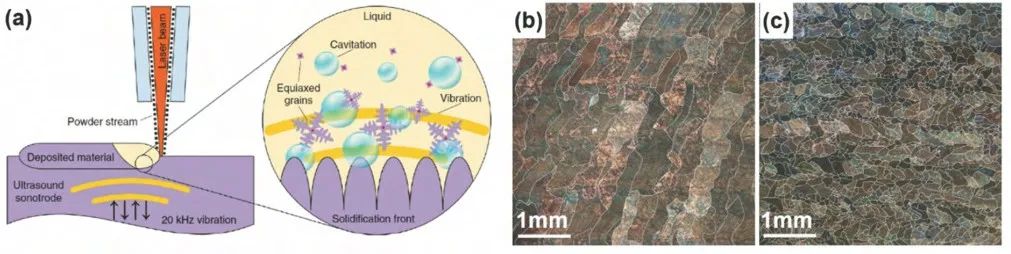
图4超声复合激光增材制造TC4合金的显微组织调控。(a)激光熔化沉积复合高频超声振动工艺示意图;(b)常规激光熔化沉积TC4合金的粗大柱状晶组织;(c)超声复合激光增材制造TC4合金的细小等轴晶组织
强度可达1450Mpa,断裂应变超过13%。笔者研究团队基于粉体完全熔化机制采用SLM工艺成形了纳米TiC增强钛基复合材料,研究后发现:TiC纳米颗粒经激光熔化及凝固析出后,形成了均匀分布的纳米层片状增强结构,并可在较宽的激光线能量密度(0.25~1.0kJ/m)下保持这种新颖的纳米增强结构,从而使激光增材制造构件具有优异的摩擦磨损性能(摩擦因数低至0.22,磨损率低至2.8×10-16m3·N-1·m-1);随着激光能量密度进一步提高,层片状纳米TiC晶粒长大,甚至发生枝晶生长而失去纳米结构,导致激光成形件的摩擦磨损性能显著降低。Attar等学者研究了TiB2增强相对SLM成形钛基复合材料显微组织及力学性能的影响规律,发现:TiB2在SLM成形过程中完全溶解于熔池中,并在后续凝固过程中以纳米级TiB的形式析出,形成新颖的Ti-TiB纳米复合材料;同时,部分硼原子固溶在层片状α-Ti中,起到了细化晶粒的作用;当加入体积分数为8.35%的TiB时,SLM成形TiB2-Ti复合材料的抗压强度可达1636Mpa,断裂应变超过17%。可见,激光增材制造特有的高能量输入、瞬间高温及超快熔化凝固过程,为钛基复合材料增强体、基体的物相与组织调控提供了热力学和动力学条件,并可使激光增材制造构件具有显著区别于铸造和粉末冶金等工艺制备的构件的显微组织及力学性能。
2.3激光增材制造镍基高温合金及其复合材料
镍基高温合金自身含有较多的合金元素,其在激光增材制造过程中普遍存在裂纹敏感性强、元素偏析严重、显微组织各向异性显著、力学性能可控性差等问题。一方面,镍基合金中亲氧能力较强的铬、铝元素易在高温作用下与成形气氛中的氧元素发生作用,形成微细氧化物夹渣,然其与基体界面间的润湿性较差,从而导致裂纹产生并降低力学性能;另一方面,碳、铌、钼等元素易在晶界聚集,显著增加低熔点共晶相的含量,加剧了热影响区热裂纹的形成。此外,各类晶界析出物会消耗镍基体中的强化相形成元素,显著降低激光增材制造镍基构件的力学性能。当前,镍基高温合金激光增材制造主要集中在Inconel系列合金上,其中沉淀强化型Inconel718和固溶强化型Inconel625的可焊接性强,亦适用于基于粉末熔化/凝固冶金过程的激光增材制造工艺。激光增材制造Inconel系列合金的组织在成形方向上为明显的柱状晶,具有较强的成形方向〈001〉织构,而在水平方向则呈胞状组织;而且,合金易在晶界析出碳化物、LaveS等脆性相。因此,激光增材制造镍基高温合金的显微组织调控主要是通过优化工艺参数进而改变熔池的温度梯度、凝固速度和冷却速率来实现的,然后结合后续的热处理工艺来实现晶粒形状、尺寸以及析出相形态、含量及分布的调控。此外,采用优化的激光扫描策略也可改变晶粒的生长织构,获得高强韧镍基合金材料。激光增材制造镍基高温合金工艺优化机制的相关研究表明:高的扫描速度和低的激光功率会导致较低的激光能量输入,故熔池熔体的黏度及润湿性较差,未熔颗粒及不规则孔隙较多,成形件表面球化缺陷也较严重;随着扫描速度减小及激光功率增大,熔体的流动性及润湿性提高,熔体铺展均匀,成形质量提升;过高的激光能量密度会增大熔体的不稳定性,易产生气孔及裂纹等缺陷,影响构件的力学性能。Wan等学者研究了激光扫描策略对Inconel718晶粒形态及织构的影响规律,发现扫描策略可以改变热流及晶粒的生长方向:进行单一线性扫描时,层与层间的热流方向相似,易形成定向柱状组织;而在层间旋转90°扫描时,热流方向不断旋转,晶粒生长竞争机制显著加强,可以获得较强的立方织构。热处理可在一定程度溶解拓扑密排相(δ相、σ相等)及碳化物等析出相,提高γ′及γ″强化相的含量,提升材料的力学性能。Zhang等学者发现SLM成形Inconel625经均匀化热处理可有效减少元素偏析,消除δ相,使组织更均匀。Sui等学者针对LMD成形Inconel718的热处理工艺进行优化后发现:在1050℃保温15min可以使LaveS相由不规则的长条状转变为细小的颗粒状,且随着保温时间延长,LaveS含量增多;长条状LaveS相易成为裂纹源,同时会使强化相γ″分布不均匀,而细小的颗粒可随基体一起变形,并起到强化作用,使试件的抗拉强度达到1341Mpa,延伸率达到19.1%。此外,基于高温高压处理的热等静压(HIP)技术可以消除激光增材制造镍基高温合金构件中的残余孔隙,抑制裂纹萌生及扩展,进而提高成形件的力学性能。由表3可知:热处理可实现激光增材制造镍基高温合金的强化,但会在一定程度上牺牲材料的韧性;同时,后处理需要合理调控加热温度、保温时间、冷却介质及热等静压的压力等参数,成本较高,工艺较复杂,缺陷形成概率也较大。
表3激光增材制造镍基高温合金及其复合材料的力学性能
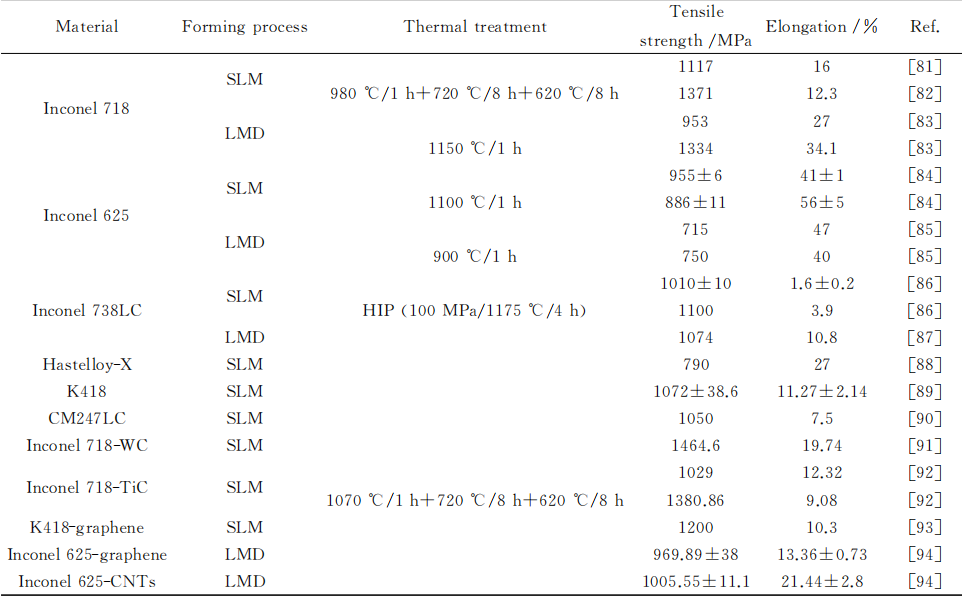
制备陶瓷增强镍基复合材料是镍基高温合金力学性能提升的另一个重要途径,可使复合材料在韧性不降低的前提下具有更高的比强度、比刚度及耐热性。Ma等学者制备了Ni/Al2O3纳米复合材料,发现添加纳米颗粒后可显著减小复合体系的热影响区而增大熔化区,如图5所示,揭示了激光作用下镍基纳米复合材料特殊的熔化、凝固特性。此反常现象主要是由于纳米颗粒会减小体系的热导率,进而降低对基板的传热;同时,纳米颗粒可增大熔体的黏度、抑制热毛细流动,进而减少熔池的热对流。笔者研究团队针对WC、TiC等微米陶瓷颗粒增强镍基(Inconel718、Inconel625等)复合材料体系,基于SLM和LMD两类激光增材制造工艺,通过激光工艺参数和复合材料组分调控,在陶瓷增强颗粒与γ基体间构建了(Ti,M)C(M为Nb、Mo)梯度界面层,有效控制并消除了界面残余应力、界面微孔及微裂纹等成形缺陷,如图6(a)所示,并揭示了激光作用下梯度界面的形成机制、显微结构特征、界面结合性能;此外,笔者研究团队还发现梯度界面可以有效改善陶瓷/基体界面的润湿行为,平衡两者的硬度差异,并可起到传递载荷、调节增强颗粒与基体变形行为的作用。笔者研究团队构建了基于增强相/基体间梯度界面设计与调控实现颗粒增强镍基复合材料构件强度和韧性协同提升的调控原理,解决了激光增材制造复合材料构件通常面临的强度升高、韧性降低这一对“强”与“韧”的矛盾。
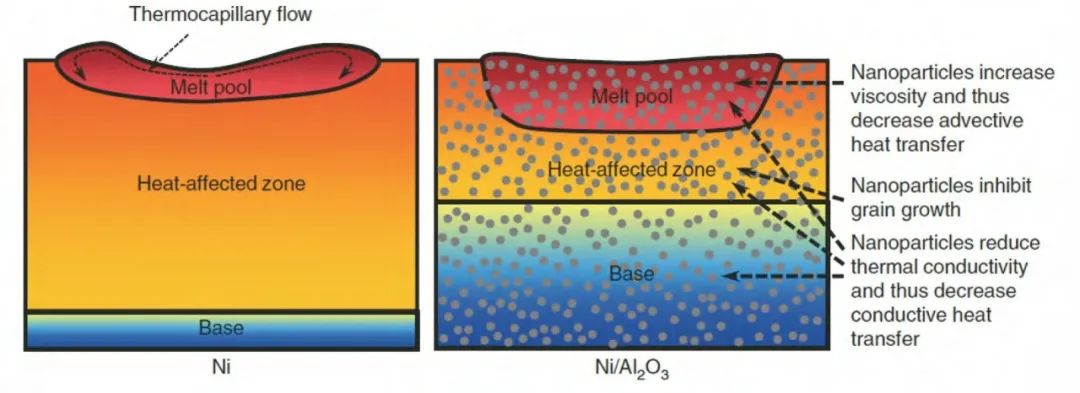
图5激光熔化镍基复合材料纳米粒子的冶金改性机制
这种在陶瓷增强颗粒与金属基体之间构建梯度界面层的工艺调控思路,在WC、TiC增强铁基复合材料激光增材制造工艺调控中也具有普适性和可行性;同时在以传统微米陶瓷颗粒为增强相的条件下,为抑制复合材料界面缺陷、提升界面结合性能及构件成形性能提供了有益的思路。Ho等学者也发现在激光增材制造WC-W2C/Inconel718复合材料中晶粒易在WC-W2C表面形核,并在界面形成扩散层,该显微组织演变源于增强相与基体之间较小的润湿角及半共格界面。另一方面,笔者团队研究后发现,纳米TiC陶瓷颗粒增强镍基复合材料的激光增材制造,可减小柱状晶及裂纹形成的概率,基体组织为胞状晶且增强相分布均匀,如图6(b)所示。这是由于纳米增强颗粒易成为基体熔体的非均匀形核点,从而提高基体的形核率,促进胞状晶形成并细化组织。基于纳米陶瓷复合及纳米改性的思路,通过激光增材制造非平衡快速熔化凝固过程中冶金热力学和动力学行为的理解与调控,可实现对纳米颗粒空间分布、晶体生长组织和形态的调控与布局,以此亦可实现激光增材制造镍基复合材料构件强度和韧性的协同提升。此外需要指出的是,当前激光增材制造复合材料构件的多功能化也是增材制造技术的一个重要研究方向,笔者通过调控激光工艺参数实现了镍基纳米复合材料表面粗糙度的调控,获得了超疏水表面,并使镍基复合材料具有优异的耐蚀性,如图6(c)所示。
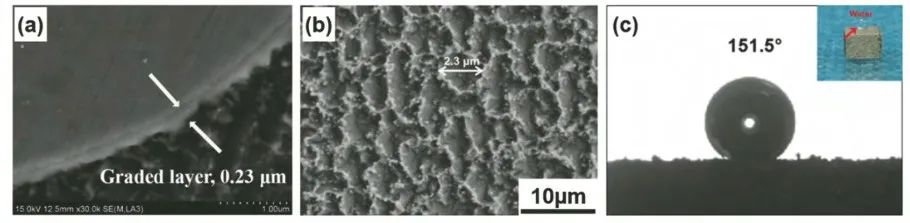
图6激光增材制造镍基梯度界面复合材料和纳米复合材料的组织与性能调控。(a)微米WC增强复合材料的梯度界面;(b)纳米TiC增强复合材料的胞状组织;(c)镍基纳米复合材料的超疏水表面
3、航空航天典型结构的激光增材制造
3.1大型金属构件的激光增材制造
应用于航空、航天、船舶、核电等现代工业的大型金属构件正朝着复杂化、一体化、高性能化方向发展,LMD技术已证实可满足大型金属构件的成形要求。LMD工艺若要在钛合金、镍基高温合金、高强钢、难熔合金等难加工金属材料大型关键构件上获得更广泛的工业应用,仍需进一步解决两大关键难题:一,高能激光长时间剧烈非稳态循环加热和高速冷却条件下,成形材料的晶粒形态及显微组织很难控制,以凝固晶粒、内部缺陷及显微组织为核心的冶金质量和性能控制是激光增材制造大型金属构件的基础难题;二,激光增材制造过程中热应力、组织应力、凝固收缩应力等多种类型复杂应力的累加与耦合,易导致大型金属构件变形,甚至开裂,大大制约了大型金属构件激光增材制造的控形与控性。
Todd研究小组在NatureMateriAlS上发文指出,增材制造技术实现工业应用的最大障碍是成形件中的热应力及多种结构缺陷。北京航空航天大学王华明院士认为,内应力及变形开裂是长期制约金属构件激光增材制造技术发展的瓶颈。钛合金密度低、比强度高、耐蚀性强,已被广泛应用于飞机发动机构件、主承力构件、起落架等,但其较差的加工性能制约了它的工程应用范围。北京航空航天大学王华明院士团队突破了飞机钛合金大型主承力构件激光熔化沉积增材制造的关键工艺技术,研制出了国际领先的飞机钛合金大型结构件激光增材制造工程化成套装备,该设备的成形室尺寸为4000mm×3000mm×2000mm。此外,该团队还实现了TA15、TC4、TC11等大型复杂整体结构主承力飞机钛合金加强框及A-100超高强度钢飞机起落架等关键构件的激光增材制造,实现了激光增材制造主承力构件的装机应用,如图7(a)所示。该团队还提出了大型金属构件LMD成形过程“内应力离散控制”新方法,形成了大型结构件内部缺陷、质量控制及其无损检验的关键技术,成形的飞机钛合金构件的综合力学性能达到或超过了模锻件。该团队建立了金属构件激光增材制造过程中凝固晶粒形态主动控制理论,实现了具有梯度组织和梯度性能的先进航空发动机钛合金整体叶盘及大型关键主承力构件的制造,如图7(b)所示。该团队制造的航空发动机钛合金叶片为定向生长的全柱状晶组织,具有优异的高温持久蠕变性能,轮盘为等轴晶凝固组织,具有优异的各向同性力学性能,如图7(c)所示。
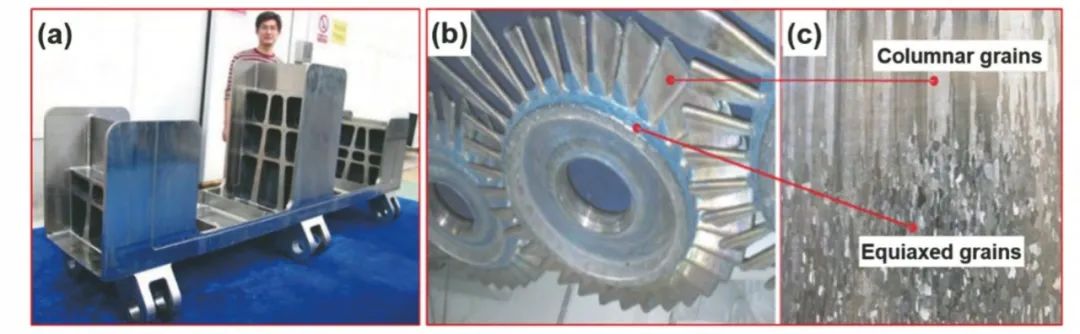
图片图7大型整体金属构件的激光熔化沉积LMD增材制造。(a)钛合金飞机大型关键主承力构件;(b)航空发动机梯度性能钛合金整体叶盘;(c)轮盘-叶片梯度过渡区的凝固晶粒组织
西北工业大学黄卫东、林鑫教授团队面向中国C919中型客机的需求,利用LMD增材制造技术制造了TC4合金体系C919飞机翼肋缘条,其长为3100mm,如图8(a)所示,探伤和力学性能测试结果皆符合中国商飞的设计要求。在构件力学性能的考核中,LMD增材制造TC4合金试件的高周疲劳性能优于实测锻件,且抗拉强度和屈服强度的批次稳定性优于3%。近年来,随着高功率激光器、高速扫描振镜等硬件的不断升级,SLM装备的研制水平持续提高,该团队研制的SLM装备成形尺寸可达600mm×600mm×600mm。采用四激光器、四振镜协同可以提升增材制造的效率,相比单激光、单振镜加工效率可提升100%~200%。大型SLM装备的发展为结构更为复杂的大型整体金属构件的成形开辟了新途径,该团队基于SLM成形的钛合金风扇叶片包边长度可达1200mm,具有复杂的空间曲面结构,且成形尺寸精度较高,如图8(b)所示;基于SLM成形的镍基高温合金发动机机匣尺寸达到了Ф576mm×200mm,为发动机关键零部件的设计、制造及应用验证提供了重要的技术支撑。
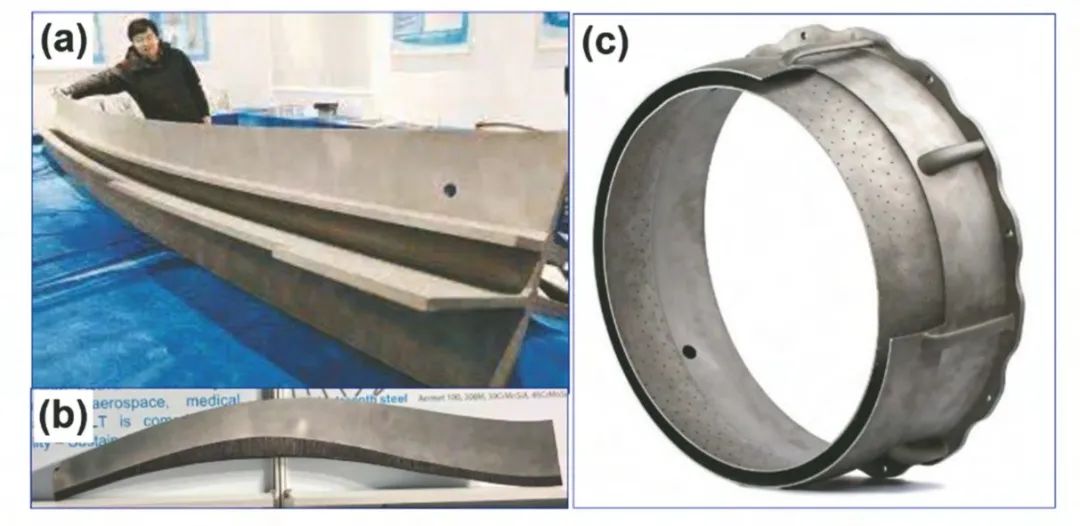
图8大型复杂金属构件的LMD及SLM增材制造。(a)LMD成形C919钛合金翼肋缘条,长为3100mm;(b)SLM成形钛合金风扇叶片包边,长为1200mm;(c)SLM成形镍基高温合金发动机机匣,尺寸为Ф576mm×200mm
3.2复杂整体结构的SLM
随着航空航天领域对热端部件服役性能要求的日益提高,整体结构的设计与制造越来越受到重视,其内含复杂内流道结构、多孔点阵结构等难加工结构,已超出传统工艺的成形制造能力,而基于SLM高精度增材制造技术可使这些复杂整体结构的快速制造成为可能。近年来,航空航天领域采用SLM技术成形的典型整体构件包括火箭推进器耐高温部件、发动机燃油喷嘴、燃烧室导流衬套等。美国国家航空航天局(NASA)和AerojetRocketdyne公司合作,基于SLM增材制造技术实现了液氧、气态氢火箭助推器的整体制造。助推器是火箭发动机系统的重要组成部分,在制造成本中占最大部分。NASA和AerojetRocketdyne公司在严格的测试环境中对激光增材制造的助推器整体结构开展了点火试验,如图9(a)所示,实现了结构减重、制造效率和服役性能的显著提升。整体结构的增材制造技术已证实对未来的空间探索至关重要。借助于激光增材制造技术,NASA提出了火箭发动机核心部件“制造速度提升10倍、生产成本降低50%以上”的目标,其基于SLM技术成形的如图9(b)所示的火箭发动机燃烧室铜衬套整体构件是其近年来的成功实践。该整体构件面向的是导电、导热性很强的铜合金,该合金是典型的激光增材制造难加工材料。该整体构件是基于GRCo-84铜合金采用SLM工艺,经258h、8255层增材制造而成的。火箭发动机燃烧室内推进剂的燃烧温度超过了2760℃,故在铜合金衬套内部一体化成形了200多个随形冷却流道,温度在-173℃以下的氢在流道中循环冷却,以防止构件在服役过程中发生熔化。对于衬套整体构件内部几何形状复杂的微细流道,其结构优化设计及激光增材制造成形质量,将直接决定发动机燃烧室的冷却效率及其服役性能和寿命。对于轻量化薄壁构件内部的一体化随形冷却流道,其延伸和布局路径受整体结构形状的约束,同时流道的尺寸和结构也制约着整体构件的激光成形性,故而向增材制造技术的发展提出了更大挑战及更高要求。
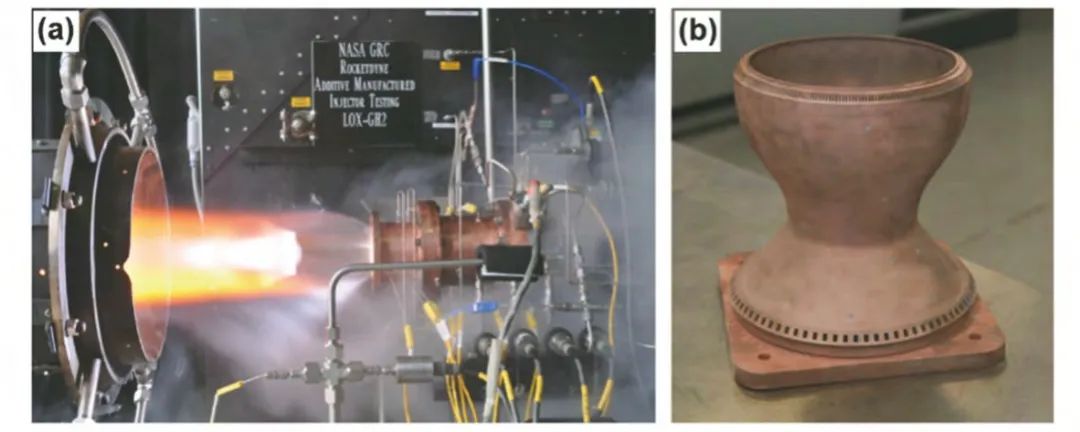
图9NASA基于SLM成形的铜合金整体构件及性能测试。(a)NASA和AerojetRocketdyne公司开展的激光增材制造构件点火试验;(b)火箭发动机燃烧室铜合金衬套整体构件
美国通用电气(GE)公司基于SLM增材制造技术研发了先进涡桨发动机(ATP)内部新型燃油喷嘴,如图10所示,这是近年来复杂整体结构增材制造航空工业应用的典型案例。燃油喷嘴一般位于发动机燃烧室之前,其主要作用是提供燃料的输送。在发动机运行过程中,空气经各级叶片的压缩之后被输送到发动机燃烧室内,与此同时燃料通过燃油喷嘴雾化或气化并被输送到燃烧室内,点火后燃料在燃烧室中充分燃烧,进而实现发动机的持续运转。因此,燃油喷嘴对加速混合气体形成,保证燃料稳定燃烧和提高燃烧效率具有重要作用。燃油喷嘴作为典型的复杂装配体,无论是成形制造还是装配组装,工序多,工装多,耗时长,成本高,且加工精度及稳定性很难达到使用要求,对于传统制造技术来说都是一大挑战。针对这一难题,GE公司采用SLM技术加工Inconel718镍基高温合金,实现了燃油喷嘴的整体设计与制造,将原先20个小部件的“组件”变成一个整体化燃油喷嘴构件,如图10(c)所示。这不仅可以消除不同部件之间冗余的连接结构,还可对燃油喷嘴结构进行优化设计,从而在从高到低的较宽燃油流量下实现良好的雾化效果,并抑制燃油雾化不充分的问题,进而减少积碳。GE公司基于增材制造技术整体设计制造的这款燃油喷嘴实现了25%的减重效果,同时缩短了制造周期,降低了生产成本,且增材制造燃油喷嘴的使用寿命提升了5倍以上。目前,GE公司这款燃油喷嘴的生产能力为每年35000~40000件,已应用在空客A320neo、波音737MAX、商飞C919和波音777-8等机型上。
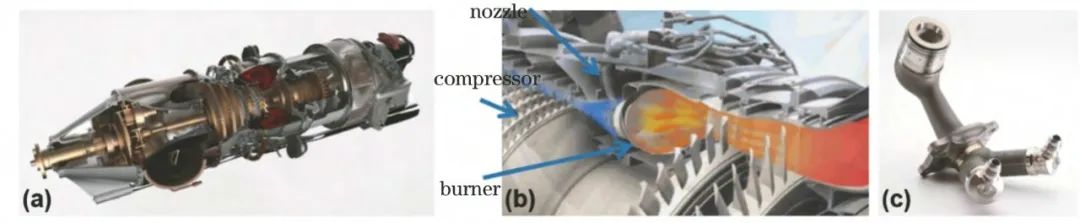
图10GE公司基于SLM技术制造的航空发动机燃油喷嘴构件[110]。(a)先进涡桨发动机(ATP);(b)燃油喷嘴在发动机内的工作原理;(c)激光增材制造燃油喷嘴构件
3.3轻量化点阵结构的SLM
对于航空航天飞行器而言,减重是永恒不变的主题,而传统制造方法已将零件减重的可能性发挥到了极致。将点阵结构优化设计与增材制造技术相结合,可使构件具有高比强度和高比刚度等优异的力学特性。激光增材制造技术因具有叠层自由制造的工艺特性,赋予了复杂轻量化结构极高的设计及成形自由度,可成形传统加工方法难以成形的轻量化复杂点阵结构。近年来,激光增材制造成形复杂构型轻量化点阵结构已成为热点研究方向之一,可为航空航天等领域轻量化金属构件性能及功能的突破带来新契机。Tancogne-dejean等美国学者将经典八隅体桁架结构应用于激光增材制造点阵结构中,设计出了在动态和静态载荷下均具有优异的能量吸收功能的八隅体金属点阵结构,成形结构在应变速率高达103S-1条件下仍具有良好吸能效果。除了将传统经典结构应用于激光增材制造点阵结构设计外,基于自然启迪的创新点阵结构设计也为构件性能带来了突破。Pham等英国学者基于金属晶体硬化机制,借鉴金属晶格微尺度结构及位错、晶界等多种强化机理,设计了一种仿晶格点阵结构,该结构相对于传统规则的点阵结构具有更加优异的耐损伤特性,如图11所示。此外,基于拓扑优化的点阵结构设计正成为金属构件轻量化及强韧化的重要途径之一。PaneSar等英国学者详尽阐述了拓扑优化技术在激光增材制造点阵结构设计方面的策略及应用,并发现经拓扑优化后的点阵结构的比刚度较传统规则的点阵结构至少提高了40%~50%。可见,增材制造技术在航空航天点阵结构产品设计与制造领域已展现出一定的发展与应用潜力,并以轻量化和高性能作为主要考核目标。
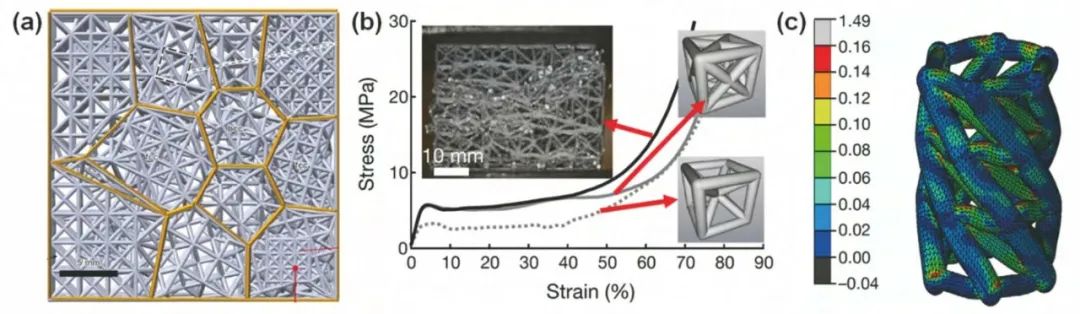
图11基于金属晶体硬化机制设计的仿晶格点阵结构的增材制造。(a)仿金属微晶格点阵结构;(b)单相与多相晶体点阵结构的应力应变差异;(c)数值模拟得到的仿密排六方晶体点阵结构(HCP)的应力分布
激光增材制造点阵构件已在国际民航客机制造领域获得了实际工程应用,空客商业飞机机舱隔板是近年来的成功案例。该结构主要用于隔离机舱乘客区与乘务员区域,同时还兼具应急担架和机组人员安全座椅的功能,如图12(a)所示,故要求该构件在保证强度的同时尽可能减重。空客公司基于SLM技术设计和制造了仿生点阵结构机舱隔板,如图12(b)所示。在成形材料上,此隔板构件选用新型轻质高强铝合金ScAlmaolly[115-116],该合金为稀土元素钪微合金化Al-Mg合金,具有较低的密度(2.67g/cm3)和良好的SLM加工工艺性能。钪元素可显著细化铝合金晶粒,故SLM成形合金构件具有优良的力学性能(抗拉强度约为520Mpa,延伸率约为13%),可作为未来轻量化结构件及点阵构件的理想材料。在结构设计上,空客研发人员基于生物启迪实现了跨尺度仿生点阵结构设计,如图12(c)所示,在宏观尺度上基于“黏菌自适应网络”算法实现了主体结构设计,该算法以最小的行数连接一组点并使每个点至少与两条线相连,因此在一条线出现失效时该点仍连接在整个设计结构中,可保障整体构件的结构完整性和结构强度。在微观尺度上,该构件借鉴了骨骼生长的生物灵感,完成了超过66000个网格的排布,实现了微观网格稠密度与应力分布相匹配,最终使得跨尺度仿生点阵构件较原蜂窝复合材料隔板结构在相同冲力下(9g重力加速度)的位移减少了8%(9mm)。在成形工艺上,该构件采用SLM技术实现复杂零部件一体化高效成形,如图12(d)所示,最终的机舱隔板构件由112个部件组装而成,相较于原蜂窝复合材料隔板构件减重45%(30kg),从而可使空客每年节省465000t二氧化碳排放量,并有望批量化应用于A320客机上。
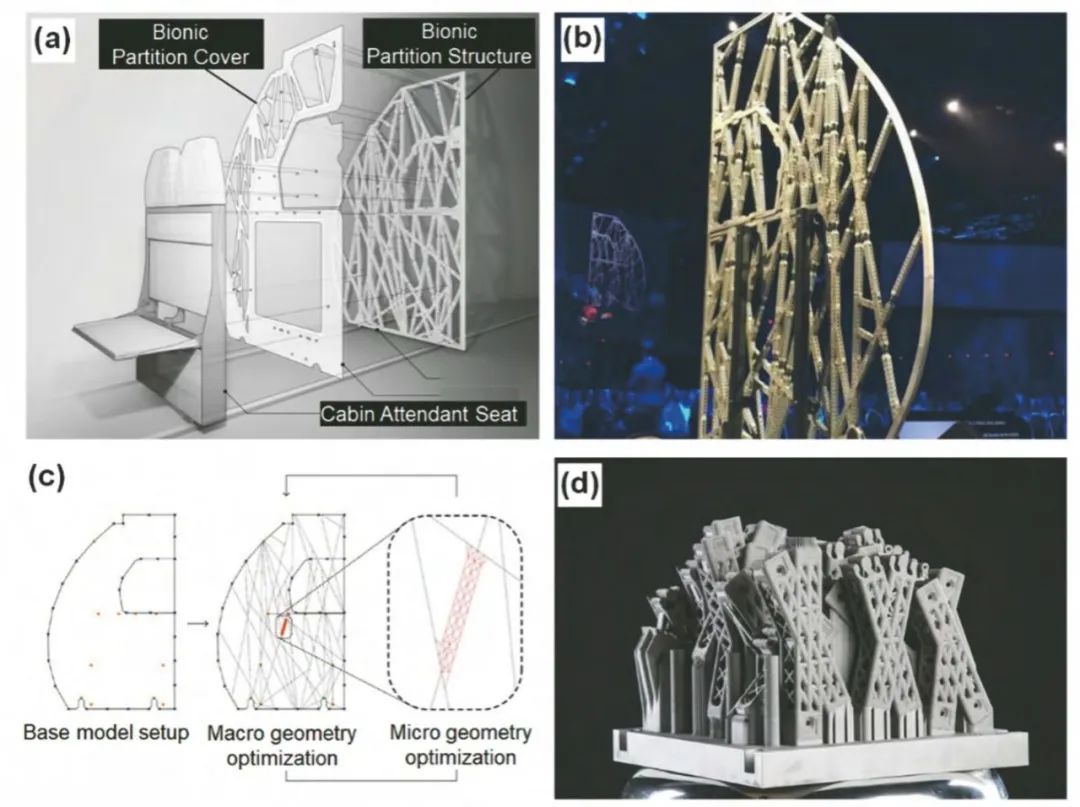
图12空客公司基于SLM技术设计制造的新型仿生点阵结构机舱隔板。(a)机舱仿生隔板结构图;(b)机舱仿生隔板实物图;(c)跨尺度仿生结构设计;(d)机舱仿生隔板零部件选区激光熔化成形实物图
3.4多功能仿生结构的SLM
激光增材制造金属构件正从高性能化向多功能化发展,Nature以“推开3D打印的限制”为题发表评述指出,材料和结构的创造将助力3D打印技术的发展,并建议“向自然界‘借’材料、‘借’结构”,道法自然,突出生物仿生(biomimicry)、生物灵感(bio-inSpired),以实现预期的功能。未来增材制造的发展将更加凸显材料的创造、结构的仿生以及多功能的集成优化。生物系统经过数十亿年的进化和自然选择,已形成并优化了其复杂的多层级组织结构,以达到最优的性能/功能来应对环境的变化。许多生物系统具有独特的多功能组合,而这往往是人工合成材料难以实现的。现代分析表征技术已证实,天然材料的优异性能或特殊功能,是依靠其内部复杂的多层次结构实现的,其尺度范围通常横跨纳米尺度到宏观尺度。对于性能/功能驱动的增材制造,基于生物灵感的仿生结构设计,是创新增材制造结构的重要途径之一,并有望实现增材制造结构性能/功能的跃升。
Nature刊发的题为《生物材料进化的启迪及其应用》综述性论文认为,生物材料蕴含着大量的源自于自然界的成分与结构信息,并指出尽管生物材料的化学成分一直是其设计关注的焦点,但对于其在非医学领域的潜在应用,应更关注其在结构拓扑优化、力学性能、功能等方面的物理属性及响应。Sciencs以《赋予远古材料新的机会》为题刊发综述性论文,该文指出,蜘蛛网所具有的高强度和高延展性的优异组合是迄今为止人工合成材料无法获取的;从材料本质上而言,蜘蛛丝实际上是一种相对简单的蛋白质,但生物结构赋予其高性能及多功能。这种基于生物启迪的结构设计与仿生优化,有望用于构建多功能的材料及构件系统。仿生的本质是学习天然结构的设计方法及材料布局,这是一个从纳/微观尺度向宏观尺度连续演变的大跨尺度结构设计。AdvancedMateriAlS刊发的综述性论文《仿生材料微/纳米制造:自然结构仿生的方法综述》”给出了仿生结构设计的一般性方法,其程序包括:基于预期获取的独特功能在生物系统中寻找生物灵感;建立跨尺度仿生结构与宏观性能/功能之间的关系;设计遴选合适的材料及工艺;构建仿生结构以实现所需的功能。同时,该论文指出仿生设计在原理上很简单,但在实际制造中却有相当难度,原因主要是多材料合理匹配与布局的挑战及微/宏大跨尺度仿生结构制造工艺的约束性。
笔者研究团队基于下一代高超音速飞行器、空间探测器等航空航天装备的整体化、多功能化发展趋势及潜在工程应用,面向减振抗冲击、隔热/防热等综合功能需求,创新发展了仿生结构及材料布局,实现了仿生结构的激光整体增材制造及其多功能化,其中涉及结构、材料、工艺、功能等多因素的耦合、匹配及一体化调控。面向减振抗冲击功能,一是考虑口足目生物口虾蛄(别称皮皮虾)尾节,如图13(a)所示,其独特的生物结构能使其抵抗竞争捕食过程中超过1500N、23m/S的冲击力,其能量吸收机理类似于沙袋,本身吸收和消散能量,而不使能量反向传递。通过解析皮皮虾尾部的宏观构型,笔者团队设计了一种仿生双向波纹板结构,揭示了高度和波长两个结构变量对仿生结构在冲击载荷作用下的比能量吸收(SEA)、冲击力效率(CFE)及应力分布的影响规律,该结构的SEA可达到45J/g,CFE最高为85%,这表明其具有优良的能量吸收能力及抗冲击稳定性。二是考虑水蜘蛛在水下构建的住所———潜水钟,如图13(d)所示,其能长时间承受不同流速、不同方位水流的冲击,具有优异的韧性和抗冲击能力,并具有桁架结构和薄壳结构的轻量化特征。针对仿生水蜘蛛潜水钟网壳结构尺寸跨度大、悬垂结构多、加工难度大等难题,笔者团队研究了网壳结构基本结构单元特征对SLM成形构件尺寸精度、致密化行为和压缩性能的影响规律,揭示了仿生网壳构件在压缩过程中的变形行为及断裂机制,并发现随着网壳支柱直径增加,主导断裂机制从应力控制断裂转变为孔隙率控制断裂。三是考虑到黄道蟹蟹钳具有密集螺旋排布的多孔道结构特征,笔者团队通过建立参数化仿生结构三维模型,基于SLM工艺研究了旋转增量和孔道分布特征对仿生蟹钳结构变形行为的影响规律;结果发现,SLM成形件截面熔池堆叠方式呈显著的螺旋特征,较小的旋转增量易导致试件在压缩过程中发生扭转破坏/失效,并发现基于仿生设计引入的孔道结构因在压缩变形过程中发生弹性屈曲而显著提高了SLM成形件的韧性。针对隔热/防热功能,考虑到挪威雪杉能在极寒环境下生存并能抵御强风的特点,笔者团队以其茎干截面显微结构为设计灵感,构建了一种兼具承载及隔热/防热功能的可重复使用的热防护结构,建立了以梯度分布的中空管为功能层并配合两个面板层形成夹层的热防护结构,该结构的热导率仅为2.321W/(m·K),比压缩强度高达98.99Mpa/(g/cm3),仿挪威雪杉热防护结构可兼具良好的力学性能和热防护性。可见,仿生设计为功能驱动的增材制造结构优化及多功能化提供了新途径,但“结构易仿、制造不易、科学更难”,其中涉及的关键科学难题包括:仿生微结构与构件典型功能的映射关系及优化模型;仿生设计的跨尺度结构激光增材制造工艺约束性及成形机制;激光增材制造仿生结构的多功能一体化评价方法及响应机制等。因此,增材制造新技术与仿生结构设计相辅相成、相得益彰,而关键科学问题的研究则贯穿于材料-结构-功能一体化的全过程各领域。
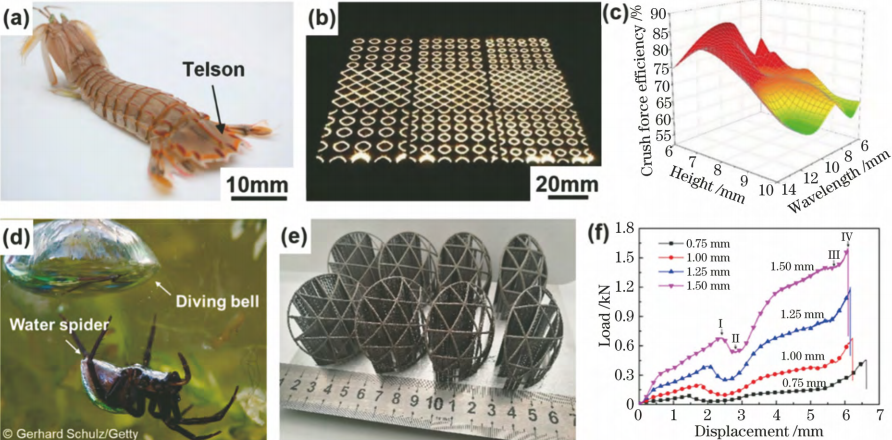
图13激光增材制造轻量化抗冲击仿生功能结构。(a)皮皮虾尾节宏观形貌;(b)仿生双向波纹板抗冲击结构SLM加工;(c)仿生双向波纹板结构高度和波长参数对冲击力效率(CFE)的影响;(d)水蜘蛛及其在水下构建的住所———潜水钟;(e)SLM成形仿生网壳结构;(f)仿生网壳结构的压缩力-位移曲线
4、结束语
增材制造具有丰富的科学内涵,主要体现在:1)围绕“增”字,涉及“工艺调控基础”,激光增材制造涉及高能激光与金属粉体的作用机理及复杂构件逐层堆积工艺的调控机制,特别是对于激光与粉末物质的作用,其尺度是几十至数百微米的颗粒量级,是一个典型的介于微观和宏观之间的“介观”尺度问题;2)围绕“材”字,涉及“材料设计基础”,主要涉及激光增材制造金属、合金及金属基复合材料的设计、制备方法及成形机制,其中激光成形材料显微组织调控是典型的“微观”尺度问题;3)围绕“制造”一词,则涉及“结构与性能/功能基础”,尤其是增材制造构件结构优化及性能/功能调控,是典型的“宏观”尺度问题。可见,激光增材制造技术的发展趋势是实现微观-介观-宏观跨尺度的材料-结构-工艺-性能/功能一体化,这是由其科学内涵所决定的。思考激光增材制造技术未来的研究与发展趋势,下列方向值得进一步关注:
1)以高性能/多功能为驱动的激光增材制造材料-结构-工艺一体化及性能/功能的主动实现。传统的材料-结构-性能/功能一体化的思路,是在选材的基础上,通过结构设计和加工工艺来获取一定的性能/功能;在这种“自上而下”的方法中,性能/功能的实现是被动的,也存在反复试凑与优化的过程。而未来激光增材制造技术的发展则可从拟实现的性能/功能出发来主动选择材料,并强调设计的广义性(除了结构设计,材料、工艺甚至性能/功能本身都需要设计)及增材制造工艺的可控性(达到高速、高效、高精度、高可靠性的效果),进而主动实现预期功能。特别是在航空航天领域机械系统复杂度不断提高、构件性能/功能集合度不断增强的发展趋势下,采用这种性能/功能驱动的“自下而上”的材料-结构-工艺一体化的思路,对于在复杂加工系统中主动实现增材制造构件的高性能和多功能化具有重要意义。
2)面向激光增材制造的“多相材料”和“多材料”设计、制备与成形,以实现将“合适的材料添加到合适的位置”。面向激光增材制造的新型二元或多元合金、纳米颗粒改性金属基复合材料、原位增强金属基复合材料等“多相材料”(mulTiphaSemateriAl)的设计与制备,是解决传统金属材料比强度和比刚度低、耐蚀性差等劣势的有效途径,而激光成形材料本身仍是均质材料。一方面,多相材料的精准设计可以通过材料设计软件和高通量实验方法加以定制,定量预测材料成分和组元对激光加工性能和增材制造构件性能的影响规律,目标是在短时间内筛选出具有预期特性及性能的多相材料,以提高激光增材制造新材料的研发成效。另一方面,随着强化相粒子(如陶瓷颗粒、稀土元素及原位形成的化合物等)相继被引入到激光增材制造高性能金属构件中,强化相的形成机制、分散状态及界面结合性能等问题制约着增材制造构件的高性能化,故可采用原位分析技术(如高速同步辐射X射线显微成像技术、中子小角散射实验技术等)研究强化相的运动与分布行为、冶金缺陷形成规律及显微组织演变规律,这对于深入理解激光增材制造材料的成形机制及性能提升机制具有重要作用。而从“多相材料”跃升至“多材料”(mulTiplemateriAlS)增材制造,则是在同一个成形构件内部的不同位置布局不同的打印材料,真正实现将“合适的材料添加到合适的位置”,以应对构件不同部位的性能/功能需求。这对激光增材制造的装备和工艺提出了变革性要求,打印装备中的粉末输运系统、铺粉系统、粉末搜集系统及对应的软件控制系统均需重新设计,以应对多材料打印的需求。同时,在打印工艺上,多材料布局依赖于对激光增材制造工艺更为精准的微/宏观跨尺度调控与优化。
3)基于激光增材制造创新结构设计,实现构件的高性能化和多功能化,以凸显“独特的结构实现独特的功能”。随着激光增材制造技术的日臻成熟,特别是面向航空航天领域的严苛的服役环境需求,成形材料及构件的力学性能已不再是唯一的追求目标,实现材料/构件的多功能化正成为重要的发展趋势。借助增材制造技术的复杂结构和多材料一体化成形能力,通过仿生结构、拓扑优化结构、超材料、超结构等创新结构设计,有望实现增材制造材料/构件在光、声、热、电、磁等功能领域的突破,甚至是颠覆。激光增材制造创新结构设计、多功能设计、多材料布局、工艺精准调控是构件实现材料-结构-功能一体化的重要方向。基于多物理场的数值模拟仿真,融合机器学习、数字孪生等新兴的人工智能技术,可为功能化材料/结构的设计与优化提供理论指导;多材料打印、微/宏观大跨尺度结构打印、多工艺混合多进程打印等创新增材制造技术的研发,可为功能化材料/结构的成形提供技术支撑。
4)面向全尺寸构件和全工艺流程的激光增材制造工艺仿真、监测及优化关键技术与方法。激光增材制造数值仿真需要考虑高能激光辐照下非平衡熔池内多相能量、动量和质量的多形式物理冶金行为,当前的数值仿真物理模型普遍为成形数道或数层的计算当量,需进一步拓宽至全尺寸构件级成形过程的热场、流场、相场和应力场的调控研究,进而需进一步合理匹配物理模型的准确性和计算效率。另一方面,需基于数值仿真方法研究增材制造构件结构特征、成形工艺、成形环境对成形质量和成形稳定性的影响规律,实现对成形质量、成形效率及潜在的成形风险等问题的预判。未来在航空航天等领域的增材制造技术研究与应用方面,应建立成形构件的材料数据、模型数据、工艺策略数据库等仿真数字平台与成形设备、成形过程监控等成形平台的数字孪生集成化,实现成形构件虚拟制造评估与生产过程仿真评估;通过机器学习建立成形设备参数、过程监控与监测指标评判方法,为激光增材制造工艺优化、成形质量提升、制造稳定性调控提供预判方法及现场技术支撑。
相关链接